- Skip to primary navigation
- Skip to main content
- Skip to primary sidebar
- Skip to footer

Supply Chain Management Design & Simulation Online

Supply Chain Case Studies
SCM Globe comes with a library of case studies that explore COMMERCIAL , HUMANITARIAN , and MILITARY supply chains. When you purchase an account you have access to all the case studies and their simulations.
The case studies range from relatively simple beginning cases like Cincinnati Seasonings , to quite challenging advanced cases such as Zara Clothing Company , or Nepal Earthquake Disaster Response . Case studies are laboratories where you apply what you learn in lectures and readings to solve supply chain problems in highly realistic simulations. Each case has a " CASE STUDY CONCEPT " showing the supply chain principles and practices highlighted in that case.
SEE WHAT PEOPLE ARE SAYING ABOUT SCM GLOBE

Case studies presently available in the online library are shown below. You are welcome to use any or all of them. You can also create your own case studies, or we can create them for you. Cases are shown in the three categories. As you work with these cases you will gain an intuitive understanding of supply chain dynamics, and develop the analytical skills for designing and managing real supply chains.
People new to SCM Globe should start with the Cincinnati Seasonings case study . Work individually at first, not in groups. Each person needs their own account. Do the three challenges shown in the online introduction to Cincinnati Seasonings. That's how you'll learn to use the software, and how to use simulations to analyze and design supply chains. Then you will be ready to work in groups or work on more advanced cases. Click on the case studies below to see a description and introduction to each case.
Commercial Supply Chain Case Studies

Collaborative Supply Chains

S&J Trading Company – Angola

Java Furniture Company – Indonesia

Cincinnati Seasonings

Supply Chains of the Roman Empire

Ancient Silk Road – First Global Supply Chain

Zara Clothing Company Supply Chain

Fantastic Corporation – Global Supply Chain

Fantastic Corporation – Unexpected Disruptions
Humanitarian supply chain case studies.

Disaster Response Supply Chains: Flooding Scenario

Nepal Earthquake Disaster Response Supply Chain

Humanitarian Supply Chains: Syria Evacuation Scenario (CIV and MIL)
Military supply chain case studies.

Burma Campaign – 1944 Invasion of India

Battle of Smolensk – 1941 Invasion of Russia

Alexander the Great Needed Great Supply Chains
New case studies.
New cases are added based on projects we do with instructors, students, and supply chain professionals. Here are the new supply chain models in the library:
- Local and Sustainable Supply Chains – Blue Ocean Cooperative
- Aerospace Manufacturing Cluster – Rockford IL
- Hyderabadi Biryani – Paramount Restaurant
- Western Desert War – May 1941
- Russian Logistics for the Invasion of Ukraine
Interactive Supply Chain Case Studies
Every case study has a main theme or concept that it illustrates. You will be challenged to use knowledge acquired in lectures and readings as well as your own real-world experience to expand and re-design the supply chains in these case studies.
In the commercial supply chain cases you need to improve and expand the supply chains to support new stores and still keep operating costs and inventory as low as possible. In cases that deal with humanitarian or military missions you need to create supply chains to deliver the right supplies to the right locations when they are needed, and do so at a reasonable cost.

We are glad to provide a free evaluation account to instructors, students and supply chain professionals interested in exploring SCM Globe simulations — click here to request an account — Get Your Free Trial Demo
See SCM Globe pricing for Academic and Business versions of the software.
The best case to start with is Cincinnati Seasonings . After working through the three challenges presented in the online introduction to this case you will be ready to handle further challenges in this case or move on to more advanced cases. Get a quick introduction to working with case studies in “ Working with Case Studies “.

As problems are found in the simulations, you make decisions about how to fix them. Make changes to your supply chain model in the Edit screen. Then go to the Simulate screen and run a simulation to see the results of your changes. Depending on the changes you make, your supply chain simulation runs for additional days and other problems arise. As you address these problems you see about how supply chains work. Apply what you learn in readings and and lectures plus your work experience to solve the problems you encounter.
Keep improving your supply chain model until you get the simulation to run for 30+ days. Then download your simulation results and create a monthly Profit & Loss Report plus KPIs (as shown below). This provides an objective basis for evaluating the merits of different supply chain solutions.

Monthly Profit & Loss Reports identify areas for improvement. They help you improve your supply chain to keep it running for 30 days and also lower operating costs and inventory levels. You can work on lowering the carbon footprint of your supply chain too. These are the challenges you address in SCM Globe, and they are the same challenges people face when managing real supply chains. What works well in the simulations will also work well with actual supply chains. Skills you develop in working with the simulations are directly transferable to the real world.
NOTE: You can run simulations for longer than 30 – 60 days, but there is usually no reason to do so. This is because most companies do not run their supply chains unchanged for longer than 30 days at a time. They use a 30 day S&OP ( sales and operations planning ) cycle and these simulations correspond to that monthly S&OP cycle. These simulations focus on the tactical realities of operating a supply chain from one month to the next, and finding what works best.
Accessing the Online Library of Case Studies
As shown in the screenshots below, logon to your account and access the case study library from your Account Management screen. Click on the “View Library” button (arrow 1) in upper right corner of the Account Management screen. In the Library screen you see a list of available supply chain case studies; click “ Import ” to load a selected case study into your account; give the imported case a Name , and click “ My Account ” to go back to your Account Management screen.
You are welcome to import any or as many of the supply chain models in the library as you wish. Once you have a copy of a supply chain model in your own account you can make any changes you want to it.

In Account Management, you “ Create a New Supply Chain ” or work with an existing supply chain by clicking the “ Edit ” button (arrow 2) next to the existing supply chain you want to work on. You can also upload copies of supply chain models sent to you by other SCM Globe users (arrow 3) , and check your account expiration date (arrow 4) .
Use the Default Values or Enter New Data
When you load any of the case study supply chain models from the SCM Globe library, they come with default numbers already plugged in. You can either accept the defaults or do some research to find more current data. This data (like data and prices everywhere) changes all the time.
Look for data on products, facilities and vehicles that are used in your supply chain and see what their specifications and costs are. Costs can vary widely in different parts of the world. Go to websites of commercial real estate brokers in cities of interest and see what you can find out about rent costs:
- for cities in North America start with www.cityfeet.com
- and for cities in other parts of the world start with www.knightfrank.com
Metric System of Weights and Measures
In the case studies all weights, volumes, distances and speeds are expressed using the metric system. The metric system is used around the world in every country except three: Liberia; Myanmar; and the United States. So it is good for supply chain professionals to feel comfortable with the metric system.
Register on SCM Globe for Access to all Supply Chain Simulations
Click the blue "Register" button on the app login page, and buy an account with a credit card or PayPal (unless you already have one). Then scan the "Getting Started" section, and you are ready to start. Go to the SCM Globe library and click "Import" next to the supply chain models you want.
- For educators
- English (US)
- English (India)
- English (UK)
- Greek Alphabet
This problem has been solved!
You'll get a detailed solution from a subject matter expert that helps you learn core concepts.
Question: From the case study titled "Half a Century of Supply Chain Management at Walmart" published by Ivey Publishing in 2013.From your understanding of the case, and in consideration of the data points provided, is the current Wal-Mart supply chain strategy (dealing directly with manufacturers, controlling the distribution, monitoring sales/transport of items
From the case study titled "Half a Century of Supply Chain Management at Walmart" published by Ivey Publishing in 2013.
- From your understanding of the case, and in consideration of the data points provided, is the current Wal-Mart supply chain strategy (dealing directly with manufacturers, controlling the distribution, monitoring sales/transport of items etc.) sustainable? Why?
Step 1: Case Study in brief:

Not the question you’re looking for?
Post any question and get expert help quickly.
- BECOME A CONTRIBUTOR
- WHITE PAPERS
- THE SUPPLY CHAIN DICTIONARY

What is Sales & Operations Planning?
The 4 supply chain metrics, static inventory an untapped source of working capital, s&op, a vision for the future. an interview with eric tinker, improving behaviours in support of world class s&op: coach for excellence.
- Planning & Forecasting Articles
How Can Data Improve Supplier Decisions
Information-based negotiations in the digital age, hurt, help or hero how to define and get more out of your most important suppliers, how to spot supplier risk during pickups & deliveries, how to spot supplier risk during on-site evaluations.
- Procurement & Sourcing Articles
The Long Tail of Inventory and Why It’s Important
No more excuses: transformative iot is staring you in the face, predictive analytics let manufacturers see more clearly into their supply chains, rise of the grocers, how 3d printing is set to shake up manufacturing supply chains.
- Manufacturing & Production Articles
6 Tips for Maximizing Efficiency and Productivity of Warehouse Operations
Robot trucks or autonomous vehicles will revolutionize the supply chain, data integration made sexy, how to avoid the most common warehouse safety hazards, out darn spot out, i say.
- Warhouse & Transport Articles
Returns – A Threat to the Bottom Line or an Opportunity to Cut Costs?
Supply chain sustainability takes root, why the 2030 sustainable development goals matter to packaging professionals, to build sustainable products, listen to your customers, getting packaging costs down to size.
- Reverse Logistics Articles
Transform Your Supply Chain For Omnichannel
The impact of maintenance operations on supply chain management, is your supply chain strategy inside-out or outside-in, how industry benchmarks can boost your asset recovery, supply chain visibility: we should be striving for more.
- Supply Chain Management articles
Accelerating the Shift to More Efficient Trucks
Insight – is it ok to lie, supply chain execution software convergence, 3d printing and the supply chains of the future, changing the production performance metric, supply chain management case study: the executive’s guide.
By Supplychainopz
Professionals in supply chain management use various methods to determine how to improve the performance of supply chain operations. Analysis of case study is certainly one of the most popular methods for people from business management background. In order to accelerate the learning, this article has gathered 20+ most sought-after supply chain case studies, analyzed/categorized them by industry and the findings are presented.

Boeing wants to encourage more flight frequency and direct route using a smaller capacity aircraft. Then they decide to outsource many things such as the design, testing and production of key components to key industrial partners and try to reduce number of components that go to assembly. The ultimate goal is to finish the final production process within 3 days. Airbus takes a bit different marketing approach. They want to utilize high capacity airplane to help airlines drive the operating cost down. They decide to selectively outsource the production of parts and keep the design and production of key components in-house.

Supply Chain of fashion industry involves a time based competition. Many customers have the unique product needs but a competition is very fierce because of the low barriers of entry. Many new players try to offer specialized products to customers all the time. This section features the supply chain case studies of H&M, Benetton, Zara and Adidas. – H&M aims to be the price leader in the fashion market.In order to materialize its vision, H&M tries to eliminate the middlemen in various stages of supply chain and consolidate the buying volumes. Product design is also the central part of its strategies. They don’t try to follow the high fashion designs but try to adopt the street trends which are easier to produce. At the end of the day, they can bring products to market within 2-3 weeks. – Benetton , in contrast, chooses to have a full control of its production but allow its licensees to operate the stores so they can focus on production and quality control. The reason is that they would like to create the worldwide brand awareness. For fast moving products, they use the production facilities in Europe. Asian suppliers will perform production for standardized products. – Zara is very famous for its time based strategy. In order to launch a new product within 15 days, Zara uses a small lot production. A new product will be tested in pilot stores. If product sales is good, a larger batch will be ordered. Otherwise, remaining products will be removed from the shelves and sold as mark-down in other stores. This creates the perception among consumers that Zara’s products are unique and you have to take it while stock lasts. Vertical integration contributes to the success of Zara, they own the majority of its production facilities and stores (this is the reason why Quick Response can be effectively implemented). Its automated distribution centers are strategically located between the center of populations so products are delivered to stores quickly. Zara also works with Air France, KLM Cargo and Emirates Air in order that they can coordinate directly with the airlines to make the outbound shipments to its stores and bring back some raw materials and semi-finished materials with return legs. The last supply chain case study in the fashion retailing industry is Adidas . In order to cope with changing customers’ demand, they decide to undertake Mass Customization strategy. The whole idea is to develop, market and deliver the product variety that most customers will find what they want. The first steps towards mass customization is to strategically offer the product choices. Too few variations will disappoint a customer but too many variations will simply postpone a buying decision. After that, Adidas asks the same key suppliers to produce custom components in order to achieve the economy of scale. In order to compensate a long waiting time, Adidas uses air freight or courier service. The reason why they can do this is that customized products are sold directly to customers so they have the higher profit margin to compensate the higher transportation cost. Supply chain strategy of the fashion retailing industry is summarized as below,

FMCG industry is typically the products sold to customers at a low cost and will be completely consumed within 1 year. The nature of this industry is the short product life cycle, low profit margin, high competition and demand fluctuation. This section will present the case studies of P&G, Unilever and Coca-Cola respectively. Forecasting and new product introduction has always been the issues for many FMCG companies, P&G is no exception. To cope with this, P&G conducts a merchandise testing at the pilot stores to determine the customer’s response to new product before the launch. The result is that the forecast accuracy is improved because a demand planner has an additional source data to make a better decision. Moreover, products can be shipped to stores in-time then lost sales is minimal. – Unilever also feels that the competition in FMCG industry has significantly increased. They have to launch the new products on regular basis but the forecasting of new product is difficult. So they create a better classification of new products (base, relaunch, repack, new) using a regression model to identify potential forecast errors for each type of new product. – Coca-Cola doesn’t really have many stock keep units when compared with other companies in the same industry. However, products go to over 2.4 million delivery points through over 430 distribution centers. Managing transportation at this scale is the absolute challenge. In order to streamline the delivery, Coca-Cola implemented a vehicle routing software. The reason is that is the software vendor has a very good relationship with Coca-Cola’s legacy ERP software vendor. Moreover, the vendor has a solid connection with the university who can help to develop the algorithm that fits in with the business’ needs. The result is that transportation planners at each distribution center can use the new tool to reduce travelling time/distance on daily basis.

Lean manufacturing concept has been implemented widely in the automotive industry so the case studies about lean manufacturing is very readily available. Due to the increasing competition in the automobile industry, car manufacturers have to launch a new model to the market more frequently. This section will show you how BMW manages a long term planning, how Ford applies lean concept to the new product development and how Hyundai manages the production planning and control. – BMW uses a 12-year planning horizon and divides it into an annual period. After that, they will make an annual sales forecast for the whole planning horizon. After the demand is obtained, they divide sales into 8 market and then select the appropriate production sites for each market, considering overall capacity constraints and total cost. As you may notice, this kind of a long range planning has to be done strategically. – Ford calls its product development system as “work streams” which include the body development, engine development, prototyping and launch process . The cross-functional team are the experts and their roles are to identify key processes, people, technology necessary for the development of new prototype. Each work stream team is responsible to develop timeline of each process. Detailed plan is usually presented on A3 sized paper. They clearly identifying current issues they are facing with supporting data, drawings and pictures. On weekly basis, they organize a big group meeting of all work stream team to discuss the coordination issues. – Hyundai deploys a centralized planning system covering both production and sales activities across the facilities and functional areas. They develop a 6-month master production plan and a weekly and a daily production schedule for each month in advance. During a short term planning (less than one month), they pay much attention to the coordination between purchasing, production and sales. Providing a long term planning data to its suppliers help to stabilize production of its part makers a lot.

Life cycle of technology products is getting shorter and shorter every day. Unlike FMCG, the launch of a new product in the hi-tech industry requires the investment in research and development quite extensively. Then, a poor planning will result in a massive loss. This section will cover JIT and outsourcing by Apple Inc, Supply Chain Risk Management by Cisco System, Technology Roadmap by Intel, Supply Chain Network Model by HP, Mass Customization by Dell and Quality Management by Sam Sung. Steve Jobs invited the Tim Cook to help to improve Apple’s Supply Chain in 1998. Jobs told Cook that he visited many manufacturing companies in Japan and he would like Cook to implement the JIT system for Apple. Jobs believed that Apple’ supply chain was too complex then both of them reduced the number of product availability and created 4 products segment, reduced on hand inventory and moved the assembling activities to Asia so they could focus on developing the breathtaking products that people wanted to buy. – Cisco Systems would like to be the brand of customer choice so they implement a very comprehensive supply chain risk management program by applying basic risk mitigation strategies, establishing appropriate metrics, monitoring potential supply chain disruptions on 24/7 basis and activate an incident management team when the level of disruption is significant. – Intel ‘s new product development is done by the process called Technology Roadmap. Basically, it’s the shared expectations among Intel, its customers and suppliers for the future product lineup. The first step to prepare the roadmap is to identify the expectations among semiconductor companies and suppliers. Then they identify key technological requirements needed to fulfill the expectations. The final step is to propose the plan to a final meeting to discuss about the feasibility of project. Some concerning parties such as downstream firms may try to alter some aspects of the roadmap. Technology Roadmap allows Intel to share its vision to its ecosystem and to utilize new technology from its suppliers. – HP ‘s case study is pretty unique. They face with a basic question, where to produce, localize and distribute products. Its simple supply chain network model is presented below,

From this example, only 3 possible locations result in 5 different way to design the supply chain. In reality, HP has more production facilities than the example above so there are so many scenarios to work with. How should HP decide which kind of a supply chain network configuration they should take to reduce cost and increase service to customer? The answer is that they use the multi-echelon inventory model to solve the problem. – Dell is one of the classic supply chain case studies of all time. Many industries try to imitate Dell’s success. The key ingredients of Dell’s supply chain are the partnership with suppliers, part modularity, vendor managed inventory program, demand management and mass customization. Also, you can find the simplified process map of Dell’s order-to-cash process as below,
– Sam Sung has proven to be the force to be reckoned with in the hi-tech industry. The secret behind its supply chain success is the use of Six Sigma approach. They studied how General Electric (GE), DuPont and Honeywell implemented six sigma. After that, they have created their own implementation methodology called DMAEV (define, measure, analyze, enable, verify). They use the global level KPI to ensure that each player in the same supply chain is measured the same way. Also, they utilize SCOR Model as the standard process. Any process changes will be reflected through an advance planning system (APS).

The last industry covered here is the general merchandise retailing industry. The critical success factor of this industry is to understand the drivers of consumer demand. Four case studies will be presented, namely, 7-11, Tesco, Walmart, Amazon and Zappos. – 7/11 is another popular case study in supply chain management. The integration of information technology between stores and its distribution centers play the important role. Since the size of 7/11 store is pretty small, it’s crucial that a store manager knows what kind of products should be displayed on shelves to maximize the revenue. This is achieved through the monitoring of sales data every morning. Sales data enables the company to create the right product mix and the new products on regular basis. 7/11 also uses something called combined delivery system aka cross docking. The products are categorized by the temperature (frozen, chilled, room temperature and warm foods). Each truck routes to multiple stores during off-peak time to avoid the traffic congestion and reduce the problems with loading/unloading at stores. – Tesco is one of the prominent retail stores in Europe. Since UK is relatively small when compared with the United States, centralized control of distribution operations and warehouse makes it easier to manage. They use the bigger trucks (with special compartments for multi-temperature products) and make a less frequent delivery to reduce transportation cost. Definitely, they use a computerized systems and electronic data interchange to connect the stores and the central processing system. – Wal-Mart ‘s “Every Day Low Prices” is the strategy mentioned in many textbooks. The idea is to try not to make the promotions that make the demand plunges and surges aka bullwhip effect. Wal-Mart has less than 100 distribution centers in total and each one serves a particular market. To make a decision about new DC location, Walmart uses 2 main factors, namely, the demand in the proposed DC area and the outbound logistics cost from DC to stores. Cost of inbound logistics is not taken into account. There are 3 types of the replenishment process in Wal-Mart supply chain network as below,
In contrary to general belief, Wal-mart doesn’t use cross-docking that often. About 20% of orders are direct-to-store (for example, dog food products). Another 80% of orders are handled by both warehouse and cross dock system. Wal-Mart has one of the largest private fleet in the United States. The delivery is made 50% by common carriers and 50% by private fleet. Private fleet is used to perform the backhauls (picks up cargoes from vendors to replenish DCs + sends returned products to vendors). Short-hauls (less than one working day drive) is also done by the a private fleet. For long-hauls, the common carriers will be used. There are 2 main information system deployed by Wal-Mart. “Retail Link” is the communication system developed in-house to store data, share data and help with the shipment routing assignments. Another system is called “Inforem” for the automation of a replenishment process. Inforem was originally developed by IBM and has been modified extensively by Wal-Mart. Inforem uses various factors such as POS data, current stock level and so on to suggest the order quantity many times a week. Level of collaboration between Wal-Mart and vendors is different from one vendor to the other. Some vendors can participate in VMI program but the level of information sharing is also different. VMI program at Wal-Mart is not 100% on consignment basis. – Amazon has a very grand business strategy to “ offer customers low prices, convenience, and a wide selection of merchandise “. Due to the lack of actual store front, the locations of warehouse facilities are strategically important to the company. Amazon makes a facility locations decision based on the distance to demand areas and tax implications. With 170 million items of physical products in the virtual stores, the back end of order processing and fulfillment is a bit complicated. Anyway, a simplified version of the order-to-cash process are illustrated as below,
Upon receipt of the orders, Amazon assign the orders to an appropriate DC with the lowest outbound logistics cost. In Amazon’s warehouse, there are 5 types of storage areas. Library Prime Storage is the area dedicated for book/magazine. Case Flow Prime Storage is for the products with a broken case and high demand. Pallet Prime Storage is for the products with a full case and high demand. Random Storage is for the smaller items with a moderate demand and Reserve Storage will be used for the low demand/irregular shaped products. Amazon uses an propitiatory warehouse management system to make the putaway decision and order picking decision. After the orders are picked and packed, Amazon ships the orders using common carriers so they can obtain the economy of scale. Orders will arrive at UPS facility near a delivery point and UPS will perform the last mile delivery to customers. Amazon is known to use Sales and Operations Planning (S&OP) to handle the sales forecast. Anyway, this must be S&OP process at product family/category level. To compete with other online retailers, Zappos pays much attention to the way they provide the services to customers. In stead of focusing on the call center productivity, Zappos encourages its staff to spend times over the phone with customers as long as they can so they can fully understand the customer’s requirements. They also upgrade the delivery from 3 days to 1 day delivery in order to exceed customer expectation.

All case study demonstrates that supply chain management is truly the strategic initiatives, not merely a cost cutting technique. Leading companies have a very strong customer focus because almost all of initiatives are something to fill the needs of customers. Relationship management is the unsung hero in supply chain management. It’s the prerequisite to the success of every supply chain. And at the end of the day, it comes down to the quality of supply chain people who analyze, improve and control supply chain operations. – See more at: http://www.supplychainopz.com/2014/04/supply-chain-management-case-study.html#sthash.MrnrGsyY.dpuf
RELATED ARTICLES MORE FROM AUTHOR
Supply Chain Minded is a very active and fast growing online community in Supply Chain for Planning, Sourcing, Manufacturing, Delivery and Reverse Logistics professionals. The Supply Chain Minded community aims to inform and connect professionals active in Supply Chain, Purchasing, Manufacturing, Warehousing, Transport, Distribution; Reverse Logistics, Service Logistics, Lean & Six Sigma, 3PL.
© Copyright - Supply Chain Minded 2024
This site uses cookies to improve your experience. By viewing our content, you are accepting the use of cookies. To help us insure we adhere to various privacy regulations, please select your country/region of residence. If you do not select a country we will assume you are from the United States. View our privacy policy and terms of use.
- Inventory Management Software
- Forecasting
- Sustainability
- Supply Chain Visibility

AI in the Retail Industry: Benefits, Case Studies & Examples
MARCH 27, 2024
Other Examples of AI in the Retail Industry AI in the retail industry is helping improve customer experiences on one hand and operational workflows on the other. The post AI in the Retail Industry: Benefits, Case Studies & Examples appeared first on ThroughPut. The result was significant: savings of €3-6.5

Supply Chain – Finance Connection: A Supply Chain Improvement Case Study
APRIL 27, 2021
Supply Chain – Finance Connection: A Supply Chain Improvement Case Study was first posted on April 27, 2021 at 7:57 am. This is a different approach to begin the journey of financial improvement using supply chain improvement projects.
This site is protected by reCAPTCHA and the Google Privacy Policy and Terms of Service apply.
Trending Sources
Talking Logistics
Logistics Viewpoints
Supply Chain Shaman
- The Logistics of Logistics
- Enchange Supply Chain Consultancy
- Enterra Insights
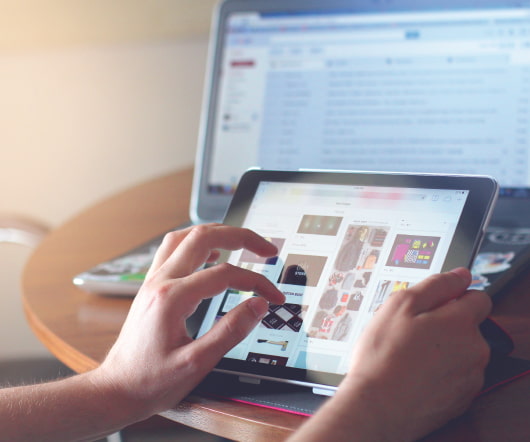
L’Oréal: A Case Study in Supply Chain Excellence
OCTOBER 5, 2018
to This is an example of managing a balanced portfolio and of driving a supply chain revolution. This case study is the best example we have seen of a customer-centric supply chain. In China, for example , more than 40% of the company’s business through eCommerce. L’Oréal’s Performance Compared to the Peer Group.
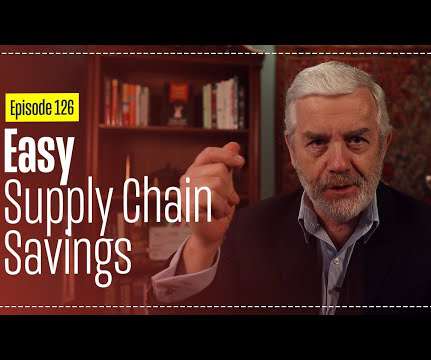
Easy Supply Chain Savings: A Simple Supply Chain Case Study
Logistics Bureau
AUGUST 31, 2021
Supply Chain & Logistics case studies are always interesting. Maybe you have some similar examples you can share in the comments? Check out this article related to this topic: 7 Mini Case Studies : Successful Supply Chain Cost Reduction and Management. And it was an easy problem to fix!
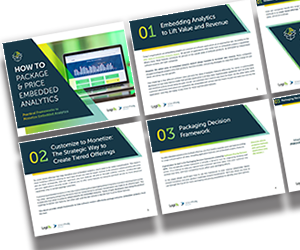
How to Package and Price Embedded Analytics
Advertisement
Just by embedding analytics, application owners can charge 24% more for their product. How much value could you add? This framework explains how application enhancements can extend your product offerings. Brought to you by Logi Analytics.
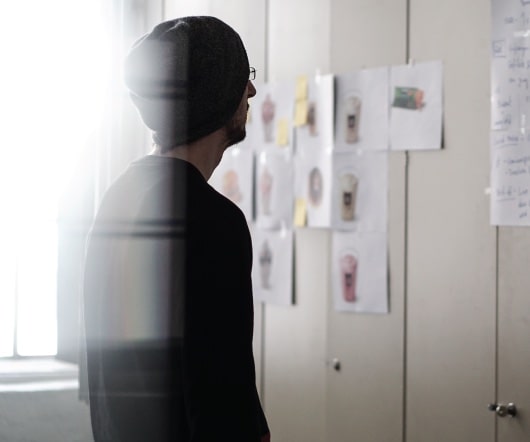
Supply Chain Case Study: the Executive's Guide
Supply Chain Opz
JUNE 1, 2014
Analysis of case study is certainly one of the most popular methods for people from business management background. In order to accelerate the learning, this article has gathered 20+ most sought-after supply chain case studies , analyzed/categorized them by industry and the findings are presented.
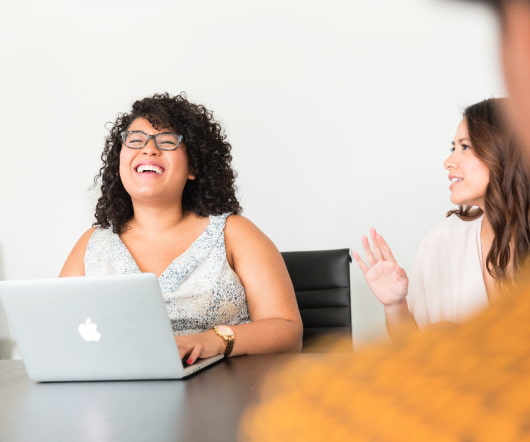
Is Apple Supply Chain Really the No. 1? A Case Study
JANUARY 7, 2013
Case Studies . A Case Study . Everything about Apple Inc is the talk of the town, for example , the new Ipad, Iphone, Apple Map or even the environmental and labor issues at its suppliers facilities. To get a closer look at the modern day supply chain at Apple Inc, this case study utilizes content analysis technique.
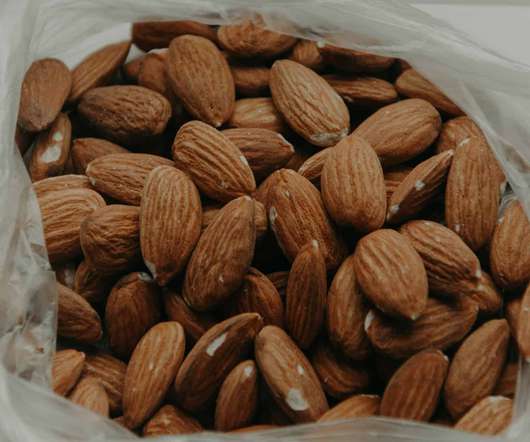
Alternative Protein: A Food Manufacturers Guide [+ Case Study]
AUGUST 12, 2021
How food manufacturers are taking advantage of the alternative protein trend: A case study One recently launched New Zealand company, Food Nation , is proving a winner in the alternative protein space. French company Ynsect, for example , farms mealworms to produce food products for humans and animals.
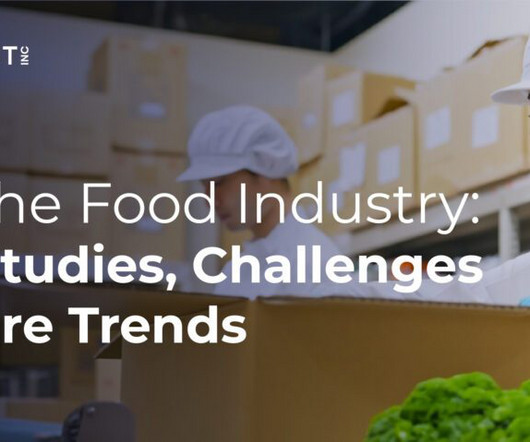
AI in the Food Industry: Case Studies, Challenges & Future Trends
MARCH 28, 2024
Case Studies of Successful AI Integration in Food Supply Chain Church Brothers Farms Church Brothers Farms, a family-owned vegetable business with a vast cultivation area of 40,000 acres, faced significant challenges due to product perishability, volatile market conditions and logistical issues, among others.
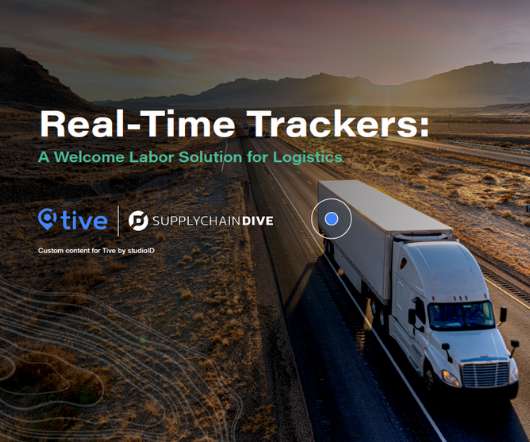

Real-Time Trackers: A Welcome Labor Solution for Logistics
Real-life case study examples of how real-time tracking helped two leading logistics providers overcome the challenges of the growing labor shortage. Why streamlining data simplifies the logistics role. The difference between real-time data tracking vs. passive data logging, and why the former is key to efficient operations.
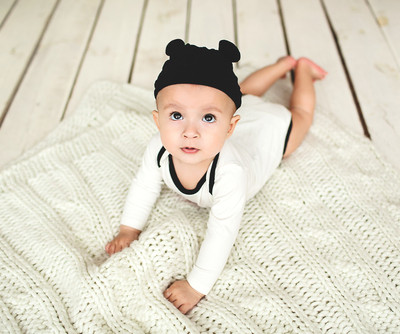
Thoughts. Selecting Supply Chain Software
APRIL 29, 2024
For example , those that actively read my blog, know that I frequently take issue with SAP, but seldom with Oracle. For example , how do you compare Arkieva to ToolsGroup ? Then build business case studies (think back to your business school case studies ) describing the opportunity. The reason? Avoid pitfalls.
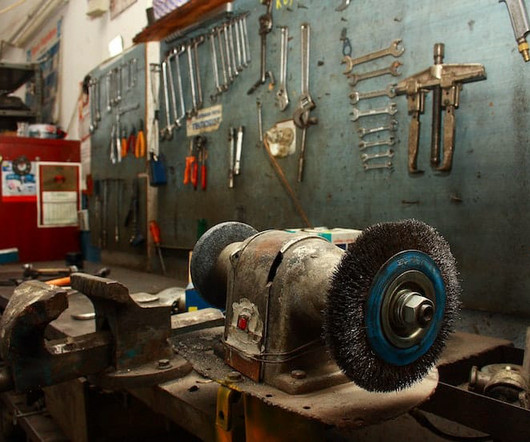
Machine Learning in Supply Chain: Definition, Uses, Case Studies
APRIL 4, 2023
We also break down several case studies of companies currently using machine learning in their supply chain processes. For example , if your customers buy large quantities of a certain product, machine learning software will be able to identify the surge in demand and feed the information back to the inventory management systems.

Lionel Racing: An Omni-Channel Case Study
JULY 19, 2016
For example , “many of our Direct-to-Consumer [drop ship] customers want everything branded as if the order is coming from them even though it’s coming from our facility,” explained Gemereth. The post Lionel Racing: An Omni-Channel Case Study appeared first on Talking Logistics with Adrian Gonzalez.

BASF Video Case Study: The Value of Real-Time Freight Visibility
MAY 3, 2018
In addition to improved customer satisfaction, Wehrle shared these examples : The data we’re getting has been hugely successful. The post BASF Video Case Study : The Value of Real-Time Freight Visibility appeared first on Talking Logistics with Adrian Gonzalez. Benefits of Real-Time Freight Visibility.
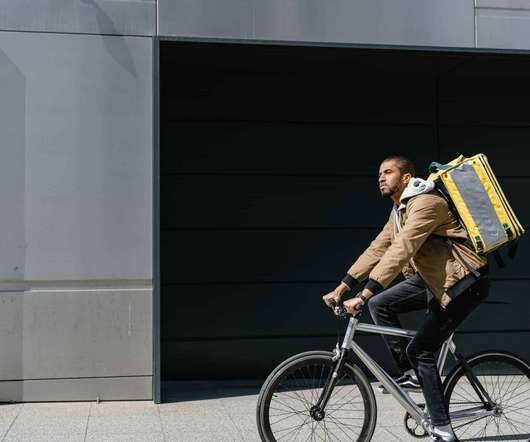
What are Dark Stores, and How do they Work? [+ case studies]
NOVEMBER 3, 2021
Here we look at how dark stores operate, how they’re profitable and why they’re on the rise – along with four examples to showcase dark stores in action. The Gorillas example shows how potential regulations to protect workers and how those workers are treated will also figure into the mix.
TMS for SMB: A Case Study with Carhartt
OCTOBER 19, 2016
Carhartt is a great example . At the end of the day, the best approach is making the effort to truly understand and address the unique needs and characteristics of every company — both today and where they’re aiming to be in the future. Gibson highlighted in her presentation, Carharrt is experiencing rapid growth.
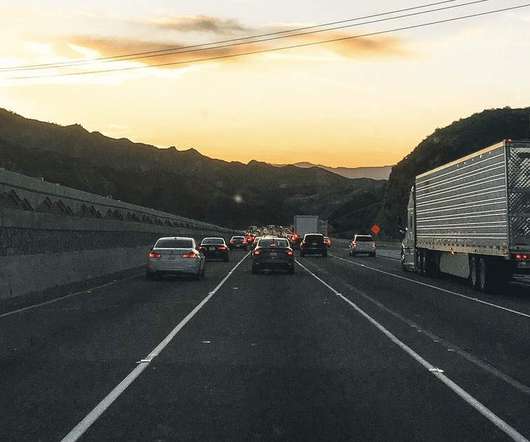
Cross Docking 101: What, Why and How? [with case studies]
SEPTEMBER 23, 2021
Time to deliver goods Cross docking can add additional time to the delivery process compared to, for example , a direct shipment strategy that involves the direct transfer to the end customer. Three case studies Cross docking strategies are used around the world and across different industries. Who uses cross docking?
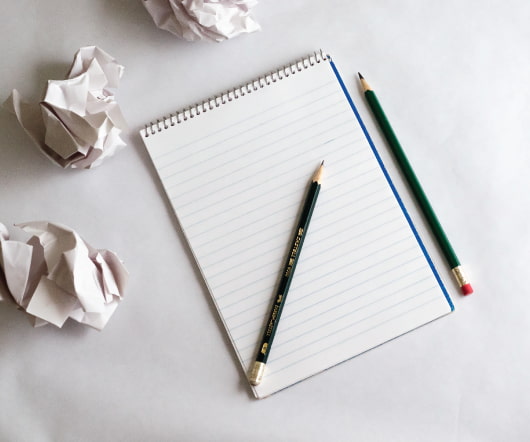
Redesign to Improve Value: A Case Study of a Supply Chain Leader
JUNE 21, 2014
For example , we discovered that transportation and duties are 5x the expense of labor and overhead. For example , people want prestige beauty from the US, Europe or Japan. Take another example – few people know where their TV was made, but the buyer cares greatly about the reliability of that product. It wasn’t that easy.
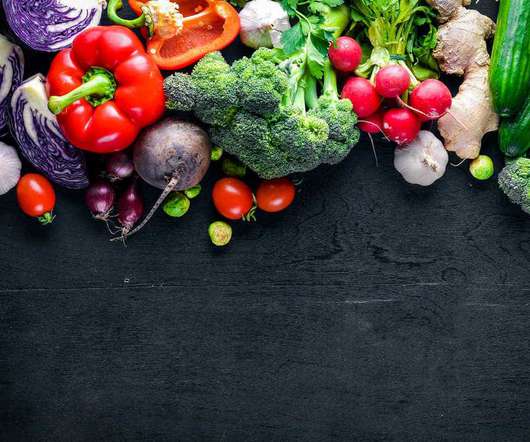
How Food Manufacturing Software Drives Profit [w Case Studies]
AUGUST 11, 2020
For example Stock Age by Stock Keeping Unit (SKU) can be cross-referenced with warehouse location to see which ingredients are sitting on the shelf and need to be moved (perhaps with a local promotion or price change). CASE STUDY 1: Gourmet Organic Herbs. CASE STUDY 2: Brandini Toffee.
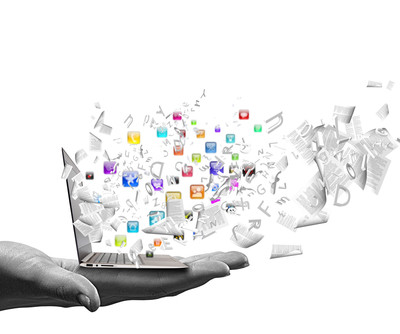
Trying to Push Content Above the Noise
JANUARY 2, 2024
Many discussions focus on driving improvement through planning, yet, when I take the client case studies on the websites of leading planning technologies and map the intersection of operating margin and inventory turns, I do not see metric improvement, sustained performance, or an increase in value. It is just accepted.
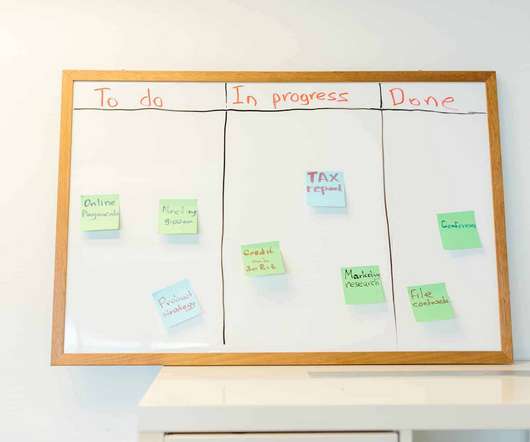
8 Examples of Kanban in Lean Manufacturing
MARCH 2, 2022
Here we give you eight real-world examples of how businesses use Kanban, a popular lean tool that’s helped companies in a huge range of sectors improve efficiency – especially those in the manufacturing industry. If you already know what Kanban is and just want the case studies , scroll down! Software development is an example .
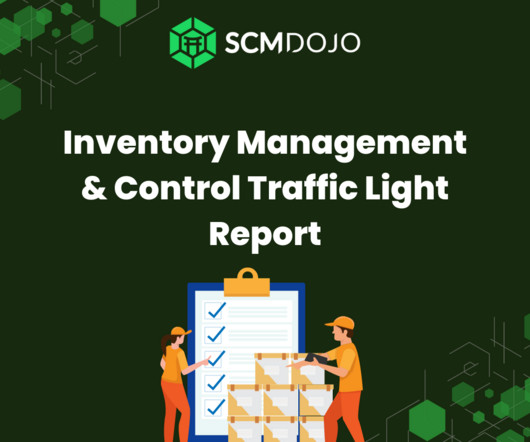
SCMDOJO vs CSCP Supply Chain Certification: My Personal Experience as a Supply Chain Professional
OCTOBER 8, 2024
It covers concepts in detail but offers very little in terms of practical exercises, real-world case studies , or detailed models. SCMDOJO offers an abundance of case studies , detailed models, and exercises that simulate the challenges professionals face daily. In comparison, SCMDOJO was designed to fill this gap.
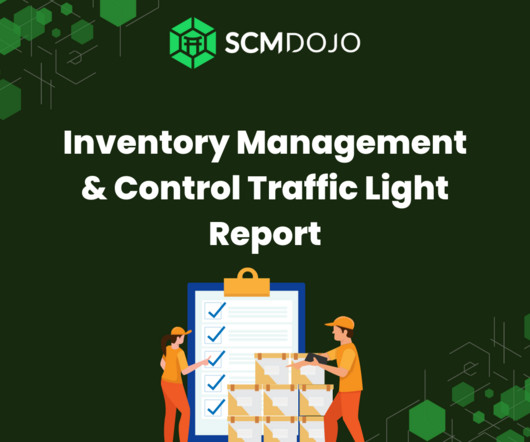
Client Case Study Video Interview
APRIL 19, 2019
Client Case Study Video Interview with Lucid Motors, Menlo Park, CA. For example , certain areas were not quite to our liking and some of the formatting we wanted to change and you were quick to do that and it made our senior management very happy. Q: Can you give me one example of how the system has saved you time and effort ?
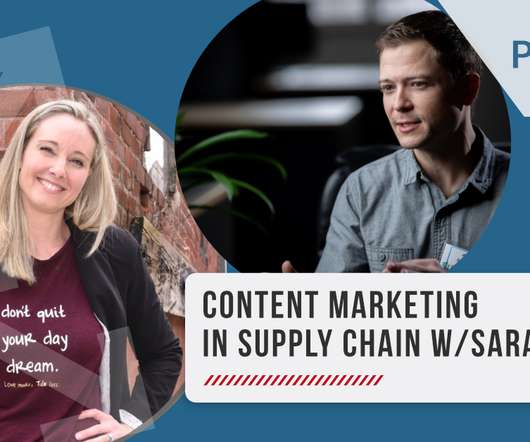
[PODCAST] The Growing “Influence” of Content Marketing in the Supply Chain
GlobalTranz
MARCH 3, 2020
Business and Marketing Resources Marketing Logistics Services: A Discussion on Getting Attention Online Listen to the Podcast Example of an Effective Transportation Management Case Study View Case Study How Industrial Companies Can Pivot to Inbound Organizations & Increase Customer Experience Listen.read More.
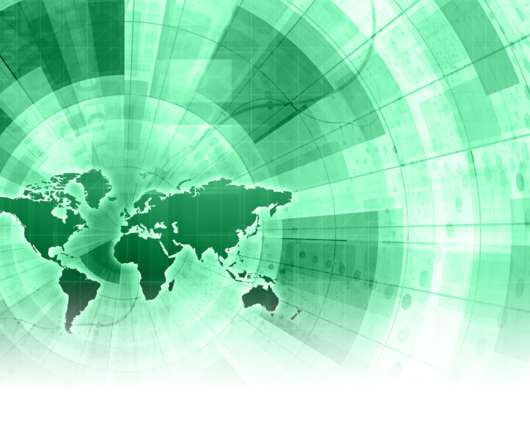
The Green Corridor: Saving Whales in California – A Case Study in Regional Collaboration
The Logistics & Supply Chain Management Society
AUGUST 19, 2022
The Green Corridor: Saving Whales in California – A Case Study in Regional Collaboration. This story is a great example of how, collaboration can happen in our fractured and decentralized commercial environment. The Green Corridor: Saving Whales in California – A Case Study in Regional Collaboration.
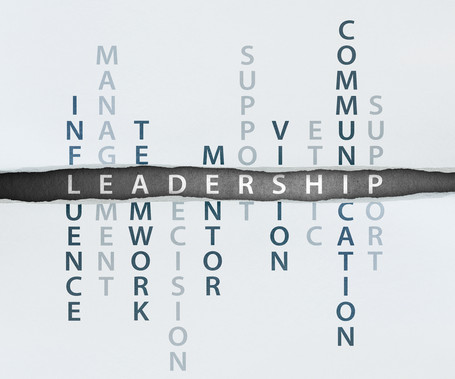
Make Room for Leadership to Drive S&OP
MAY 13, 2024
For example , in the research, I found maturity in Cadbury, DuPont, and Gilette processes. One of my favorite case studies was Campbells in 2014. See the World Kitchen case study in the Agility Report. This research, completed in 2006, was during the transformation of multi-national to global supply chains.
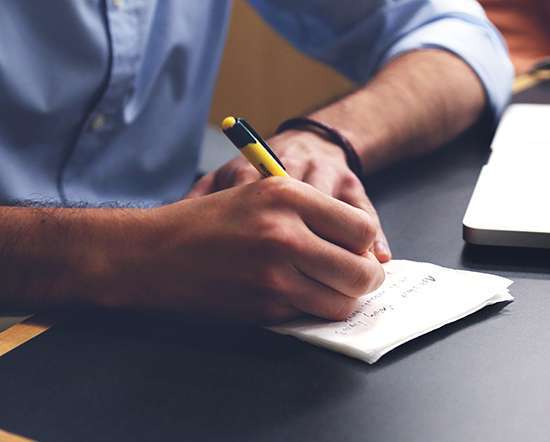
Surgery Center Case Study: Less Time at Computer, More Time in OR
FEBRUARY 6, 2019
We now know, on a real-time basis, whether a contract has expired, for example . The post Surgery Center Case Study : Less Time at Computer, More Time in OR appeared first on Hybrent. In addition, Hybrent ensures we’re staying in compliance on contracts. Ready to Update Your Supply Chain? Request a Demo.
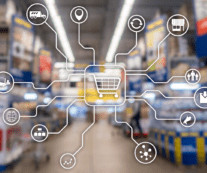
Understanding the Profitability of Omnichannel Retail is a Problem
NOVEMBER 20, 2023
But one thing you notice as you go to omnichannel software vendor’s web sites and examine customer case studies , the case studies may talk about retailers growing their revenues by 100% or more, but none talk about how much profitability grew. These new order fulfillment paths allowed retailers to rapidly grow sales.
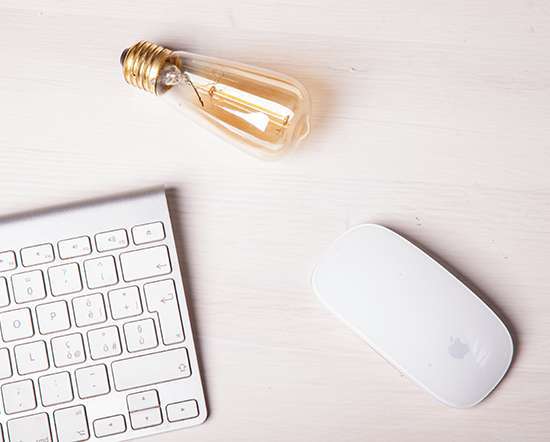
Examples of How Supplier Quality Management System Implementations Pay Off
JUNE 11, 2015
We conclude our series on supplier quality management (SQM) today with a look at some case studies and examples of benefits derived from the application of a supplier quality management system. Examples and Case Studies from the Implementation of a Supplier Quality Management System.

The Best Websites To Learn Supply Chain
NOVEMBER 17, 2024
Pros Cons Expert Monitoring No free practical tools Availability of newsletter No free podcasts Highly theoretical Offer less practical & real-world examples Read More About CIPS onDemand VS SCMDOJO Here Udemy Similarly, Udemy offers a wide range of courses that need more structure.
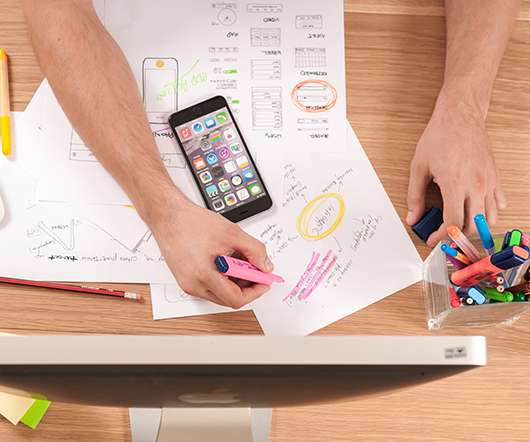
A Case Study in Reverse Logistics Optimization!
Supply Chain Game Changer
NOVEMBER 23, 2018
“This has been an excellent example of how ModusLink can deliver measurable value for our computing and hardware clients,“ explains ModusLink’s Vice President of Global Client Development. The post A Case Study in Reverse Logistics Optimization! Learn more at [link]. Check out Reverse Logistics and the Power of Your 3PL!
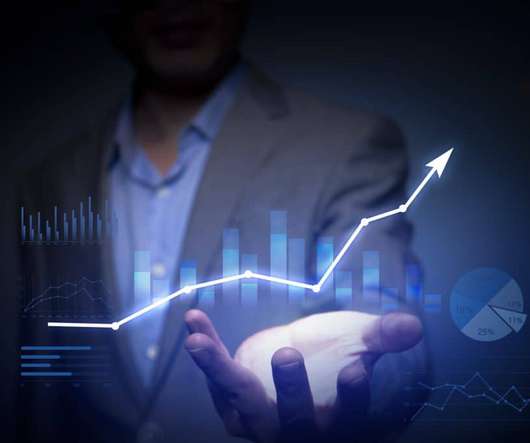
JAGGAER Webinar with Accenture Strategy and Attijariwafa Bank Case Study: Accelerating Trust in Banking – Internal, Suppliers and Customers
OCTOBER 22, 2020
A case study presentation by Youness Taghrichte provided a good example of how JAGGAER customers in the financial services sector are tackling these issues. Attijariwafa Bank has successfully implemented a source-to-contract solution with the JAGGAER ONE platform.
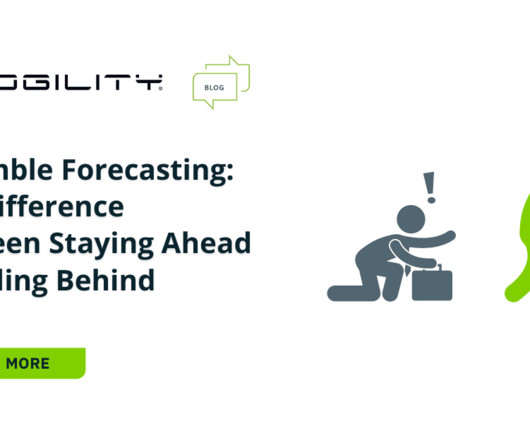
Ensemble Forecasting: The Difference Between Staying Ahead or Falling Behind
AUGUST 19, 2024
In this article, we delve into the benefits of employing ensemble modeling for demand forecasts, backed by examples and data. Example : Consider a retail company that experiences sudden demand spikes during holiday seasons. For example During the COVID-19 pandemic, demand patterns underwent rapid and unprecedented changes.

Melitta: Collaborating for an Improved Forecasting Process
NOVEMBER 2, 2020
For example , within an audit workflow multiple stakeholders across various regions can apply detailed market knowledge specific to their regions to the demand baseline forecast for a more accurate result. Read the full Melitta case study below. Read Case Study . Michael Youssef.
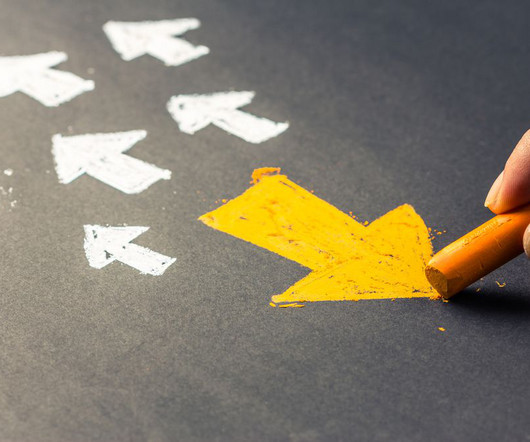
Elevating The Voice of the Supply Chain Contrarian
JUNE 21, 2023
Many of the case studies being presented at today’s conferences were born during the pandemic and the post-pandemic turbulence. For example , Monster Beverages beats Coca-Cola and PepsiCo, while Celanese outperforms Dow Chemical. While companies talk digital, the projects follow traditional supply-centric paths.
New Case Study on Alcatel-Lucent Sustainable Procurement Best Practices
JULY 9, 2015
Case Study . We are pleased to publish a new case study detailing Alcatel-Lucent’s sustainable procurement program. Download the Case Study from the library. Long-time EcoVadis client, Alcatel-Lucent, has done all this and more.
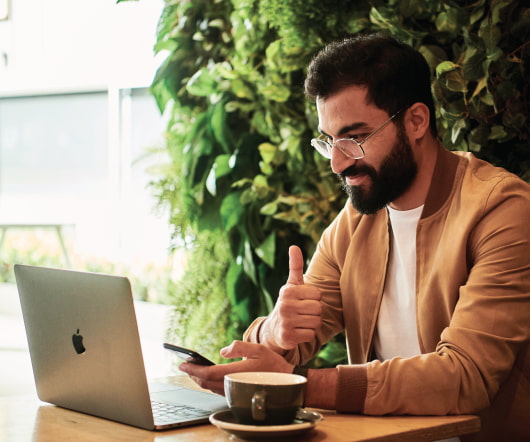
Unlocking the Value of Global Supply Chain: the Case Studies
JULY 7, 2014
For example , they make it easier for customers to locate products during shopping, pick the products, checkout, bringing products back home and install the furniture. Their unique selling points are products with good design at lower prices. To drive cost down, Ikea shifts some of their activities to customers or self service operating model.
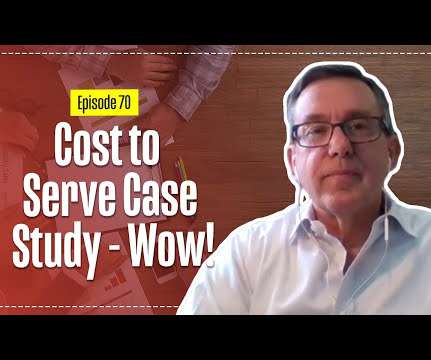
Cost to Serve Case Study that was Off the Scale! – with Steven Thacker
JULY 21, 2020
A Great Example . Let us watch the video below: Related articles on this topic have appeared throughout our websites, why not check them out? Robobyrne: Cost To Serve Lesson. Supply Chain Secrets: What is Cost to Serve? – Best Regards, Rob O’Byrne. Email: [email protected]. Phone: +61 417 417 307.
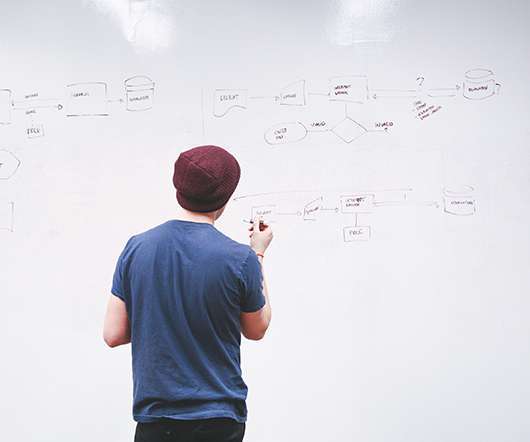
Case Study: How Generac Power Systems Cut Millions from Its Global Transportation Spend
CH Robinson Transportfolio
MARCH 28, 2018
For example , Generac works with our global forwarding and port services experts to optimize containerized freight moving from the West Coast to Chicago and beyond. The post Case Study : How Generac Power Systems Cut Millions from Its Global Transportation Spend appeared first on Transportfolio.
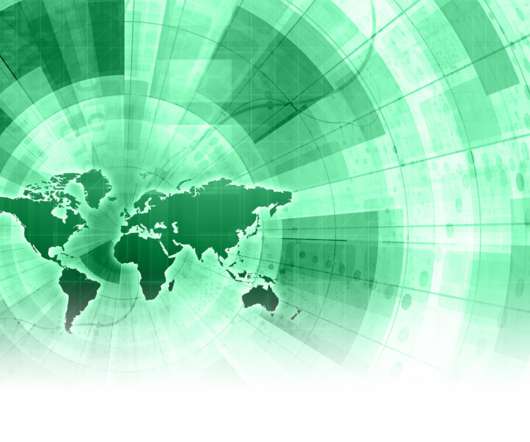
The Green Corridor: To Realise the Circular Economy Dream – Reach Out to Your Community
NOVEMBER 22, 2022
In one example , Crust Group in Singapore provides a Southeast Asian example of a cross industry “circular economy” partnership. In my compost example , I save on buying fertilizer (along with all the processing, packaging and transportation associated with it). This is the challenge that industries face all around the world.

The Critical Path: Navigating Supply Chain Efficiency in the Oil Industry
JUNE 27, 2024
Crisis Management Strategies for Unforeseen Disruptions Developing robust crisis management frameworks ensures that companies can respond swiftly and effectively to supply chain disruptions.
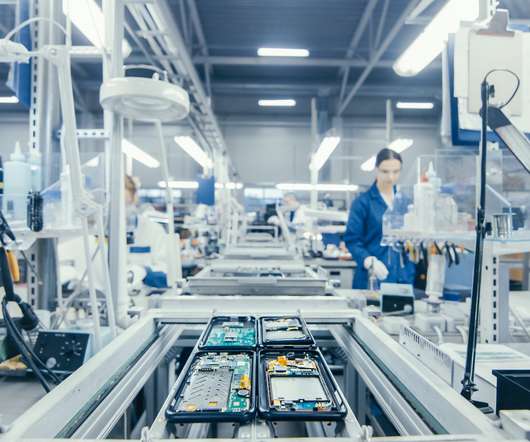
Optimization and Execution: How Manufacturing can lead the Industry Renaissance
DELMIA Quintiq
JUNE 9, 2020
Companies that were unable to meet these challenges have been left behind (for example , in High Tech think Blackberry and Compaq). In numerous case studies , manufacturers have found that the limited visibility to shop floor activities and poor planning led to problems with over-scheduled machinery and equipment.
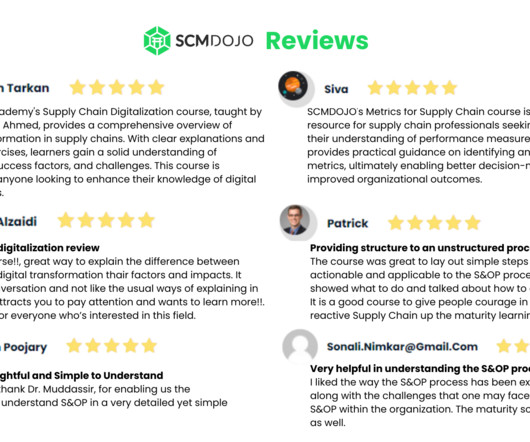
LinkedIn Learning vs SCMDOJO: Which Online Learning Platform is Right for You?
MAY 27, 2024
The courses are designed to provide practical skills with real-world examples , case studies , and exercises, allowing you to apply what you learn in your professional life. SCMDOJO’s interactive learning features, such as quizzes and case studies , are seamlessly integrated into the platform.
Stay Connected
Join 102,000+ Insiders by signing up for our newsletter
- Participate in Supply Chain Brief
- How to achieve six-figure benefits from digitizing paper-based supply chain operation
- 2019 Supply Chain Brief Summer Reading List
- Stay At Home Reading List
- Add a Source
- Add a Resource
- 2018 Supply Chain Brief MVP Awards
- 2019 Supply Chain Brief MVP Awards
- 2020 Supply Chain Brief MVP Awards
- 2021 Supply Chain Brief MVP Awards
- 2022 Supply Chain Brief MVP Awards
- Mon. Nov 25
- Sun. Nov 24
- Sat. Nov 23
- Fri. Nov 22
- Nov 16 - Nov 22
- Warehousing
- Procurement
- Transportation
- Supply Chain
- More Topics

Input your email to sign up, or if you already have an account, log in here!
Enter your email address to reset your password. a temporary password will be e‑mailed to you., be in the know on.
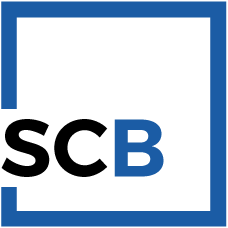
Supply Chain Brief
Expert insights. Personalized for you.
We organize all of the trending information in your field so you don't have to. Join 102,000+ users and stay up to date on the latest articles your peers are reading.

Get the good stuff
Subscribe to the following Supply Chain Brief newsletters:
You must accept the Privacy Policy and Terms & Conditions to proceed.

You know about us, now we want to get to know you!
Check your mail, we've sent an email to . please verify that you have received the email..
We have resent the email to
Let's personalize your content
Use social media to find articles.
We can use your profile and the content you share to understand your interests and provide content that is just for you.
Turn this off at any time. Your social media activity always remains private.
Let's get even more personalized
Choose topics that interest you., so, what do you do.
Are you sure you want to cancel your subscriptions?
Cancel my subscriptions
Don't cancel my subscriptions
Changing Country?
Accept terms & conditions.
It looks like you are changing your country/region of residence. In order to receive our emails, you must expressly agree. You can unsubscribe at any time by clicking the unsubscribe link at the bottom of our emails.
You appear to have previously removed your acceptance of the Terms & Conditions.

We noticed that you changed your country/region of residence; congratulations! In order to make this change, you must accept the Aggregage Terms and Conditions and Privacy Policy. Once you've accepted, then you will be able to choose which emails to receive from each site .
You must choose one option
Please choose which emails to receive from each site .
- Update All Sites
- Update Each Site
Please verify your previous choices for all sites
Sites have been updated - click Submit All Changes below to save your changes.
We recognize your account from another site in our network , please click 'Send Email' below to continue with verifying your account and setting a password.
You must accept the Privacy Policy and Terms & Conditions to proceed.
This is not me

IMAGES
VIDEO
COMMENTS
Case studies are laboratories where you apply what you learn in lectures and readings to solve supply chain problems in highly realistic simulations. Each case has a " CASE STUDY CONCEPT " showing the supply chain principles and practices highlighted in that case.
Explore TEC's proven, data-driven approach to aiding companies through their crucial supply chain management (SCM) system software selection and implementation ventures, focusing on critical areas like evaluation, selection, implementation oversight, and vendor contract negotiations.
Our expert help has broken down your problem into an easy-to-learn solution you can count on. Question: Chapter 07 Case Study P.165- Operations and Supply Chain Management 15th edition: Circuit Board Fabricators, Inc. is a small manufacturer of circuit boards located in California near San Jose.
From your understanding of the case, and in consideration of the data points provided, is the current Wal-Mart supply chain strategy (dealing directly with manufacturers, controlling the distribution, monitoring sales/transport of items etc.) sustainable? Why? There are 2 steps to solve this one. Not the question you’re looking for?
In order to accelerate the learning, this article has gathered 20+ most sought-after supply chain case studies, analyzed/categorized them by industry and the findings are presented. Aerospace Industry is characterized by high material costs (about 65-80%).
Browse Case Study and Examples content selected by the Supply Chain Brief community.