Thank you for visiting nature.com. You are using a browser version with limited support for CSS. To obtain the best experience, we recommend you use a more up to date browser (or turn off compatibility mode in Internet Explorer). In the meantime, to ensure continued support, we are displaying the site without styles and JavaScript.
- View all journals
- Explore content
- About the journal
- Publish with us
- Sign up for alerts
- Published: 11 January 2024

The forefront of chemical engineering research
- Laura Torrente-Murciano 1 ,
- Jennifer B. Dunn 2 ,
- Panagiotis D. Christofides 3 ,
- Jay D. Keasling 4 , 5 , 6 , 7 , 8 , 9 , 10 ,
- Sharon C. Glotzer 11 ,
- Sang Yup Lee 12 ,
- Kevin M. Van Geem 13 ,
- Jean Tom 14 &
- Gaohong He 15
Nature Chemical Engineering volume 1 , pages 18–27 ( 2024 ) Cite this article
15k Accesses
10 Citations
26 Altmetric
Metrics details
To mark the inaugural issue of Nature Chemical Engineering , we asked a collection of scientists working in different branches of chemical engineering to share their perspectives on the challenges and opportunities that lie ahead for their respective fields.
You have full access to this article via your institution.
Chemical engineering provides a versatile framework for solving complex and often coupled systems-oriented challenges. In this Viewpoint, nine expert scientists working in different branches of chemical engineering share their perspectives on the opportunities that lie ahead for their respective fields. The topics are diverse, covering a wide range of systems, processes and scales. However, a common voice is clear: core chemical engineering principles are necessary to overcome many of the most pressing scientific and societal challenges in quantitative and practical ways. These principles are indispensable in maximizing efficiency, developing and controlling processes, improving costs, and reducing environmental impacts and labor demand. Here is what they said.
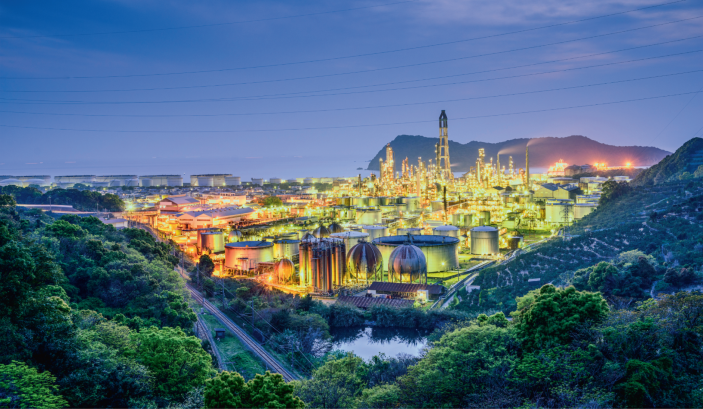
Laura Torrente-Murciano: redesigning the chemical industry for net zero
There has not been a more exciting time for chemical engineering (and related disciplines) in over 60–70 years. Governments and companies worldwide are responding to severe environmental, social and political pressures by setting ambitious net-zero targets within the next 25–30 years. This rapid timeline will witness not only a profound transformation of our energy landscape but also a fundamental reshaping of the entire chemical industry, an industry currently providing more than 60,000 products (ranging from fertilizers to pharmaceuticals, polymers and many others) that underpin almost every single aspect of our twenty-first-century lifestyle.
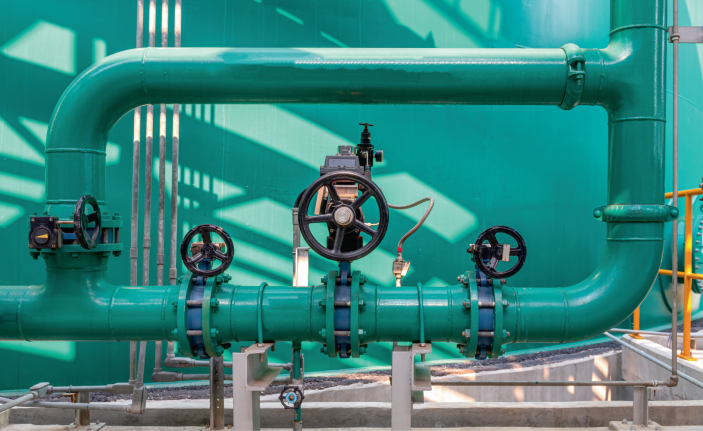
The roots of the (petro)chemical industry lie in an era characterized by cheap and abundant fossil fuel energy in the first half of the twentieth century where little was known of the effect of greenhouse gas emissions on the climate. Many of the core processes used to manufacture the industry’s platform chemicals (such as olefins, aromatics, methanol and ammonia) rely on high temperatures and pressures, often necessitating energy-intensive separations. Improvements, optimizations and integrations have been consecutively developed, with most of these processes achieving high efficiencies, but the key unit operations have largely remained unchanged.
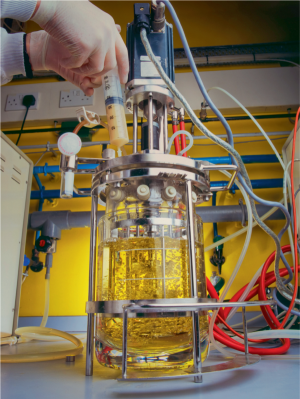
Even though the (petro)chemical industry accounts for only approximately 7–9% of the global fossil fuel consumption, two compelling factors are driving a redefinition of its future. Firstly, achieving net-zero scenarios necessitates negative carbon dioxide emissions, meaning that the carbon embedded in products should be of non-fossil origin (scope 3 emissions). Secondly, the oil fraction (naphtha) currently feeding the chemical industry will become economically prohibitive with the decarbonization of the transport and energy sector.
These two key environmental and economic drivers are underpinning the onset of a new, greener chemical industry shifting from the current use of fossil fuels as energy and feedstocks to sustainable feedstocks powered by renewable energy (so-called power-to-X). Central to this revolution is the development of new conversion processes that utilize biomass (including algae), carbon dioxide, recyclable materials (mainly plastics), air (as a nitrogen source) and water (for hydrogen production) for the synthesis of conventional platform chemicals as well as new ones, ultimately leading to alternative, reusable, recyclable and biodegradable end products. The recent literature clearly illustrates the massive academic efforts in this realm, with some new potentially green processes currently being scaled-up and even commercialized 1 . Further acceleration can be enabled by knowledge transfer of emerging catalytic strategies for the activation of C–C, C–O and C–N bonds, mechanisms, and catalyst design principles between different non-fossil feedstocks 2 .
Equally important is the development of energy-efficient separation processes in the context of the whole chemical process, opening the door to novel process integrations and operating conditions 3 . New selective and robust materials, coupled with deeper mechanistic understanding, are poised to facilitate the widespread deployment of well-known adsorption, absorption, membrane and crystallization operations, moving away from energy-intensive thermal separations (mainly distillation, evaporation and drying) that currently dominate the chemical industry and consume approximately 10–15% of the global energy 4 .
The abovementioned advances will undoubtedly be built on the same chemical engineering principles we have today, yet, they will usher in significant paradigm shifts. For example, in many power-to-X processes, the energy production will be considered within the chemical process boundaries, blurring the limits between the chemical and energy industries, with complete integration in off-grid processes. Unlike the existing model of continuous (fossil) energy supply, new processes will need to adapt to the seasonal and year-to-year fluctuations in renewable energy supply, necessitating innovative solutions beyond conventional buffering methods (for example, using batteries). Economic optimizations may indicate the need for flexible operation (for example, processes capable of swiftly adjusting production capacity), marking a departure from the conventional steady-state operation 5 . Achieving this flexibility in production demands novel control strategies, resilient catalysts and construction materials under cyclic conditions, and smart scheduling protocols, hitherto unfamiliar to the chemical industry. Similarly, new heat integration approaches will be needed as well as the development of novel heat storage and heat transfer approaches beyond the current reliance on steam.
The diffuse nature of renewable energy and its demand for large surface areas for its production may also influence the configuration of the future green chemical industry, leading to smaller processes and more distributed, local manufacturing. The conventional economy-of-scale principle may give way to the capital expenditure utilization index 6 , where sector coupling assumes equal importance, albeit in a different form.
Finally, the training and education of the next generations of chemical engineers (and related disciplines) will be pivotal to achieve all these transformations. Creativity, ingenuity and clear vision will be essential to create new processes and models while valorizing current assets as much as possible to bring new and old players into this exciting, challenging and much-needed evolution of the chemical industry.
Jennifer B. Dunn: systems- and community-level thinking to address societal challenges
The discipline of chemical engineering holds the keys to unlocking a society that regenerates rather than degrades the environment. It is important to recognize this potential while acknowledging that the discipline has also contributed to creating technologies and products that degrade the environment. Plastics are a prominent example. They bring about benefits including reducing food waste and safeguarding sterile surgical instruments. Yet, eliminating plastic pollution is one of the grand challenges of our time. Recently, chemical engineers and others have raced to develop technologies to recycle plastics that aren’t widely recyclable today and to invent new, easily recyclable polymers.
A second example is energy. Chemical engineers have been central to the oil and gas industry, which has provided services including heating homes and fueling vehicles to transport goods and people. Combustion of transportation fuels, however, contributes 28% of US greenhouse gas emissions 7 . The natural gas industry emits 23% of US national methane emissions 7 . At present, chemical engineers are central to the transition to lower-emitting energy sources. For example, the discipline is fundamental to devising improved ways to make, transport, store and use hydrogen 8 , especially ‘green’ hydrogen made with solar- or wind-derived electricity. Moreover, it is foundational in designing the energy storage systems that will allow society to harness intermittent renewable energy sources.
Chemical engineering is unique in its systems thinking approach to solving these challenges. Chemical engineering students explore process design trade-offs and learn that every choice launches ripple effects with advantages and drawbacks. Over their careers, chemical engineers continue to grapple with trade-offs, making design decisions often without complete information.
This training and career experience uniquely situates the discipline to guide technology research and development towards commercially viable energy sources, chemicals, plastics and other products that offer environmental benefits. Chemical engineers are well positioned to apply tools including techno-economic assessment (TEA) and life-cycle analysis (LCA) to achieve these aims. These tools can quantify technologies’ commercial promise and sustainability benefits. In the case of emerging technologies 9 , these tools are often built on process models that must capture to the extent possible how the technologies might operate at scale. From these models, the same type of parameters (such as energy, solvent, raw material and water consumption) that are used in the process economics calculations every chemical engineering student learns can support the calculation of LCA metrics such as life-cycle greenhouse gas emissions and water consumption.
I believe that it is incumbent upon chemical engineers to deploy these tools such that the solutions we advance for solving challenges such as the climate crisis and plastic waste — among many others — offer environmental benefits from cradle-to-grave. For example, if a plastics recycling technology that recovers monomers is more energy intensive than monomer production from virgin raw materials, that technology either should be further developed to cut energy consumption or set aside in favor of technologies that do offer life-cycle environmental advantages. Furthermore, replacing fossil fuel feedstocks with bio-based feedstocks does not always result in lower life-cycle greenhouse gas emissions 10 . LCA is essential for evaluating whether such technology shifts can offer the improvements they may promise qualitatively.
Opportunities for chemical engineers to improve TEA and LCA of emerging technologies abound. Firstly, improving our ability to model energy and material demands for emerging technologies, including electrochemical processes, energy storage material design and manufacturing, technologies to recover nutrients from wastewater, low-energy separation technologies, carbon dioxide utilization processes, chemical plastics recycling and synthetic-biology-based chemical synthesis, to name a few, is essential. Ideally, improved models will be open source to benefit the entire research community. Furthermore, identifying promising emerging technologies requires a solid understanding of today’s chemical, materials and energy industries. Data limitations, however, hamper our ability to develop a high-fidelity baseline 11 . Coming together as a community across industry, academia and government to fill these data gaps is important. In addition, our community should encourage early-stage researchers to address the commercial viability and environmental benefits of their technologies quantitatively, transparently and using the frameworks of TEA and LCA. Such efforts will allow the field to prioritize technologies with the most potential for positive impact. Finally, our discipline should actively engage with communities where it is possible that new technologies and infrastructure — such as H 2 pipelines or plastics recycling facilities — may be established. Proactive action on the concerns communities express can increase their safety, health and quality of life. Community engagement and systems-level thinking are fundamental to our discipline’s central role in moving towards energy, materials and chemical systems that are regenerative rather than detrimental to the environment and society.
Panagiotis D. Christofides: engineering learning-based algorithms for process control, safety and cybersecurity
In industrial chemical plants, raw materials are converted to desired end products via processes that must be safely operable, adhere to environmental regulations, meet product specifications and be economically viable, all of which are achieved by the implementation of advanced automatic process control systems. Traditionally, model predictive control (MPC), a constrained optimization-based control method that is the gold standard employed in advanced control of chemical processes, is formulated with data-based linear dynamic models, and is used to compute control actions to maintain optimal process operation while accounting for process and control actuator constraints. However, several limitations exist in the linear MPC framework. Specifically, many chemical processes are inherently nonlinear due to Arrhenius dependence of reaction rates on temperature and complex catalytic reaction mechanisms, and thus, they often require nonlinear dynamic models to be adequately modeled and effectively controlled. Furthermore, it is often desirable to be able to explicitly account for safety concerns (for example, pressure or temperature in a reactor must not exceed certain limits) in the control system design. In addition to these long-standing issues, the rapid proliferation of networked sensor and actuation devices in the context of the Industry 4.0 revolution has made cybersecurity a growing concern that requires novel approaches to be handled. This piece will highlight exciting recent advances in tackling these challenges and unresolved issues where chemical engineering expertise is needed to address them.
While first-principles-based modeling provides a direct way for nonlinear dynamic process model development, it may be cumbersome and difficult to implement in complex industrial processes that may also not be well understood from a fundamental physicochemical standpoint. As an alternative, data-based machine learning (ML) modeling, with emphasis on recurrent neural network configurations trained using time-series data and ensemble learning schemes, provides a new paradigm for nonlinear dynamic model development that can be used in the implementation of nonlinear MPC systems. Recent work has established the theoretical foundations of this approach 12 , and in a subsequent work, a recurrent neural network was used to model and control an experimental electrochemical reactor using process data 13 . Despite this progress, dataset construction and pre-processing, network construction using process-specific knowledge, network error quantification and real-time update are important, unresolved issues that are crucial in the field of ML-based MPC. While nascent research efforts have already been dedicated to these problems, a significant set of challenges remains to be addressed. The recent use of statistical ML theory provides a general framework for deriving error bounds on the generalization capabilities of common types of neural network, but needs to be developed further.
In addition to revealing nonlinear dynamic process relationships from data, ML tools can address classification problems such as the ones arising in the context of process operational safety as well as fault diagnostics and prognostics, thus providing a broad array of topics where ML can make an impact. Process operational safety is possibly the most crucial reason to implement controllers in a chemical process, because, for example, if the temperature or pressure within a reactor exceeds its material limits and leads to an explosion, the results can be catastrophic in terms of lives, the environment and capital. To incorporate safety directly into the controller design, advanced formulations of MPC (such as a control-Lyapunov-barrier-function-based MPC 14 ) have been proposed, which allow the delineation of specific, unsafe regions of operation to be avoided by the controller, the knowledge of which may be obtained from operators and engineers. While such methods typically require a priori knowledge of a well-defined region in the operating space, ML-based classification methods can identify such unsafe regions from process operational data, regardless of the complexity of the unsafe region, and should be explored further.
In the current era of big data, process safety is also strongly linked to the control system security as control systems that utilize an array of networked sensors and actuators are vulnerable to cyberattacks. Intelligent cyberattacks that are aimed at deteriorating closed-loop performance without destabilizing the process can require advanced defensive methods such as ML-based detectors that employ neural networks to detect and classify these attacks 15 . To further secure control systems, the networked communications within the system may also be encrypted to establish cyber-secure networked communications 16 . However, due to the high complexity and computational cost of MPC for large-scale processes, decentralized and distributed ML detectors and MPC using encrypted networked communications may be needed, requiring further research in this direction.
In conclusion, the era of the development and implementation of ML tools in process control, safety and operations has begun, and it promises to dramatically improve our ability to operate and control industrial chemical processes.
Jay D. Keasling: engineering biochemical factories for natural products
Natural products are a rich source of therapeutics, flavors and fragrances, colorants and dyes, health supplements, cosmetic ingredients, and more. Many of these molecules are derived from plants (for example, artemisinin to treat malaria, paclitaxel and vinblastine for certain cancers, cannabinoids for epilepsy, opioids for pain and the saponin QS-21 as a vaccine adjuvant), have multiple stereocenters, and are oxidized and functionalized in multiple locations. Generally, these molecules accumulate to minute quantities in the natural producer, thus requiring significant resources (such as land and water) to produce them. While synthetic chemistry routes to most of these molecules have been developed, these routes contain many low-yielding steps and are thus uneconomical even for these very expensive molecules.
Over the past two decades, chemical engineers and others have refactored biosynthetic pathways for these complex natural products into microorganisms to simplify the production process, reduce cost and synthesize unnatural derivatives that would not be possible using the vegetal production process 17 , 18 , 19 , 20 . These engineering efforts are akin to the development of catalysts and chemical factories that chemists and chemical engineers have developed over decades to convert petroleum feedstocks into useful chemicals. Just like building a complex chemical factory, there are many challenges in refactoring biosynthetic pathways from plants and other organisms into an industrial microbe, including elucidating the biosynthetic pathway in the native producer and expressing the genes that encode the pathway enzymes at the appropriate levels and during the ‘best’ phase of cell culture growth. There are several examples where chemical process control theory has been applied to the development of genetic systems to control expression of heterologous genes, but there remains much work to make these genetic control systems like the sophisticated chemical-plant-wide control systems now used in chemical factories.
In plants and other eukaryotes, complex natural products are often synthesized in multiple tissues and organelles, moving from organelle to organelle to be oxidized, decorated, protected and deprotected, much like unit operations in chemical factories. As such, eukaryotic microorganisms (such as Saccharomyces cerevisiae ), which have many of the same organelles, are often the chosen production hosts; expressing the enzyme in the same or similar organelle in the production host as it is expressed in the native producer seems to be the best strategy for ensuring successful pathway implementation 4 . Just as piping is needed to move chemical intermediates between unit operations in chemical factories, transporters (a type of chemical pipe) are needed to move intermediates into and out of organelles. Unfortunately, transporters are often missing or not discovered when a biosynthetic pathway is elucidated 19 . Indeed, the development of inter-organelle transporters is another area that needs chemical engineering treatment.
Many of the pathway refactoring efforts initially result in low titer, rate and yield of the desired product, making these processes just as uneconomical as the synthetic chemical routes. Owing to the lack of predictability in engineering biological systems, iterative cycles of design, build, test and learn are used to deduce metabolic bottlenecks, improve enzymes, and balance gene expression and metabolic fluxes to improve titer, rate and yield. Chemical engineers have developed much of the theory and models to identify pathway bottlenecks and ways to improve production of the desired product. More recently, machine learning techniques have been developed to further improve data analysis and pathway design, but much more work is needed 21 . As biological design software improves and more well-characterized biological components become available, fewer design, build, test and learn cycles will be necessary to achieve high titer, rate and yield, moving the development of microbial chemical factories closer to other engineering disciplines, such as chemical engineering.
Numerous other challenges exist in scaling engineered microbes from bench-scale units to large bioreactors. There are several examples of engineered organisms failing to perform in large bioreactors as they were engineered to perform in the laboratory. Nevertheless, several companies have made significant progress in scaling engineered microorganisms to produce natural products 22 . While chemical engineering departments were the typical places where bioprocess engineers were trained, the relative dearth of such training has forced many companies to train their own bioprocess engineers. This trend needs to be reversed by placing bioprocessing research on equal footing to microbial host engineering, which will in turn encourage academic institutions to hire individuals to train the next generation of bioprocess engineers.
Chemical engineers have contributed mightily to the development of microbial factories for natural products. However, there remain many challenges in developing more efficient factories and scaling them for industrial production, something that the chemical engineering discipline is well suited to undertake.
Sharon C. Glotzer: assembly engineering for materials systems by design and on demand
It is said that human civilization is defined by the materials available to us. From the Stone Age to the Bronze Age and the silicon age, what we achieve as a society depends on our ability to master materials. What materials will define humankind in the future? And what is the role of chemical engineering in realizing these materials?
By combining advances in cross-cutting fields such as nanoscience, complex systems, network science, process engineering, biophysics, artificial intelligence and advanced manufacturing, exciting new technologies and solutions to humankind’s greatest challenges will be enabled not by a single material but by materials systems — integrated collections of materials building blocks that combine many properties and behaviors in ways not possible today. Tomorrow’s materials systems will be multifunctional and carry out tasks, with complexity of function emerging through the collective behavior of the system components. Materials systems of the future will be made by design and on demand wherever and whenever they are needed, using readily available resources. Materials systems designed for building strong, stable structures or flexible, adaptive clothing will also carry electrons and information. They will process logic operations locally and acquire robotic abilities such as actuation and locomotion. Materials systems no larger than a red blood cell will make possible in situ diagnostics and treatments for disease. Importantly, materials systems of the future will be programmed to disassemble into recyclable components when no longer needed.
Chemical engineers are positioned precisely at the nexus of all the disciplines, tools, technical approaches and analytical thinking that will make this future possible. Transport processes, statistical thermodynamics, kinetics — these core concepts in chemical engineering are central to the materials systems of the future. As chemical engineers, we are learning how to design, synthesize and assemble materials building blocks into complex structures. We are considering how to scale up the processes that will be needed to make materials systems useful and practical, and how to make them, sustainably, at low cost using ubiquitous source materials at point of use. We are designing systems driven far from equilibrium, consuming energy as biological systems do, and we are designing ways to power these new materials systems and processes to transport heat and fuel in and out of them.
Nanoparticle building blocks provide a unique route to new, functional multimaterial systems 23 . Over the past two decades, nanoparticle synthesis has advanced from making small numbers of imperfect particles from a few exemplar materials to making nanoparticles of exquisite shape and tight size polydispersity from a variety of starting materials 24 . Functionalizing colloidal nanoparticles with molecular ligands conveys valency to the particles that controls their local arrangements. Shape alone conveys valency through entropy in crowded nanoparticle suspensions. Together, particle shape and interaction anisotropy imbue particles with entropic and enthalpic patchiness, respectively, that can be tuned to achieve the desired valency 23 , 25 . In this way, these patchy particles act as ‘atom equivalents’ that can be engineered precisely and without the quantum constraints that accompany atomic valency. Already we can envision a future where patchy particle building blocks will be made by the bucket, from any material, in any shape, and functionalized in a myriad of ways so that any local valency can be engineered by design. Using inverse methods, theory and computer simulation can optimize these particles for assembly into target structures 26 .
So, if we can make any building blocks we want, how do we engineer the ones we need to assemble into the materials system we want — by design and on demand? This question is the purview of assembly engineering 27 . Just as the foundational chemical engineering subject of reaction engineering describes the processes by which reactants combine (through chemical reactions) to form products, assembly engineering describes the processes by which building blocks combine (through assembly) to form an organized materials system. Assembly engineering seeks to engineer the shapes of constituent building blocks and their interactions at the nanoscale, exploiting coatings and molecular linkers as glue to coax nanoparticles to arrange into structures whose hierarchical order spans length scales from nanometers to millimeters and more. In assembly engineering, we engineer both entropy and enthalpy to achieve structural and functional complexity across atomic, molecular and colloidal scales. By integrating nanoparticles made of different materials — noble metals, rare earths, plastics, semiconductors and quantum dots — into a single complex particle system, their assembly can be controlled to organize the various constituents into strategic relative positions, making possible the integration of multiple properties and functionalities in a single materials system. Importantly, the materials system approach will make possible the integration of otherwise antagonistic properties and behaviors. Through the coupling of plasmonic, magnetic and other properties of small nanoparticles, new emergent behaviors that lead to new technologies are inevitable.
Sang Yup Lee: metabolic and bioprocess engineering for sustainable production of chemicals
Recently, metabolic engineering and bioprocess engineering have taken center stage in the sustainable production of chemicals from renewable, non-food biomass or carbon dioxide. To make bioprocesses competitive, it is essential to develop microbial strains and fermentation processes that allow the highest possible titer, productivity and yield from the most suitable, accessible and inexpensive carbon sources 28 , 29 . Thus, chemical engineers play an important role in developing optimal bioprocesses by considering the upstream (raw material preparation and strain development), midstream (fermentation) and downstream (recovery and purification) processes together. In particular, the microbial strain, which significantly affects the overall performance of the bioprocess, needs to be developed with the entire bioprocess in mind.
To this end, chemical engineers have adopted knowledge from a wide array of themes, ranging from microbiology, molecular biology and biochemistry to chemical reaction engineering, transport phenomena, and process design and simulation. Following the chemical engineering strategies of overall process optimization, metabolic engineering has also evolved into systems metabolic engineering. This approach begins with techno-economic analysis and performs strain development through integrated consideration of host strain selection, metabolic pathway design, metabolic flux optimization, fermentation process development including scale-up, and downstream processes 29 . Similar to chemical process design, computational and in silico techniques such as genome-scale metabolic modeling and simulation as well as bioprocess design have greatly facilitated the development of high-performance microbial strains and bioprocesses. At the cell-factory level, these approaches suggest optimal flux distributions at a system-wide level, enabling efficient pathway engineering. Like many other fields, systems metabolic engineering and bioprocess development are increasingly utilizing data science and artificial intelligence (AI), including generative AI, to facilitate the design and construction of enzymes and pathways and the optimization of bioprocesses. These advanced technologies will be collectively employed to further enhance the development of microbial strains and bioprocesses, as well as to automate the engineering process.
The above approaches have enabled the efficient bio-based production of industrially important chemicals including dicarboxylic acids (malonic, succinic, glutaric and adipic acids), diamines (1,3-diaminopropane, putrescine and cadaverine), diols (1,2-propanediol, 1,3-propanediol, 1,3-butanediol, 1,4-butanediol, 2,3-butanediol and 1,5-pentanediol), lactams (butyrolactam, valerolactam and caprolactam), and others 30 . It is anticipated that a growing number of chemicals and materials will be produced through the use of engineered microorganisms, thereby replacing their petrochemical counterparts. Various microorganisms have also been engineered to produce biofuels, including bio-gasoline, biodiesel, bio-jet fuel and biogas 30 . The production of short-chain alcohols (ethanol, propanol and butanol) and short-chain alkanes, which can be blended with or used as a substitute for gasoline, has been successfully accomplished. Also, oleaginous microorganisms, such as Rhodococcus opacus and Yarrowia lipolytica , have been metabolically engineered to produce fatty acid ethyl esters and hydrocarbons from non-edible lignocellulosic biomass. This approach reduces our reliance on plant oils for manufacturing diesel and jet fuel, which are used as food sources and would otherwise compete with them. This is crucial because for the next several decades, there will be no viable sustainable solution for aviation other than ‘sustainable aviation fuel’.
Moving towards sustainable bio-based production of chemicals, fuels and materials is crucial, but again we cannot ignore the economic factor 31 . The target performance metrics must be defined based on the target product (for example, high versus low price and high versus low volume). Carbon sources should be carefully selected, considering availability, logistics and cost, with a focus on utilizing abundant and inedible biomass feedstocks. Metabolic engineering has also enabled the utilization of one-carbon compounds, such as carbon dioxide, as carbon sources for cell growth and chemical production. Challenges in direct carbon dioxide conversion include low solubility and efficiency, which can be addressed by using methanol or formic acid synthesized from carbon dioxide. For example, several microorganisms have been metabolically engineered to grow on a one-carbon substrate as a sole carbon source 32 . The advancements in direct microbial carbon assimilation present the potential for carbon-neutral or carbon-negative production processes, especially when combined with direct air capture technologies. The fermentation medium plays a crucial role in performance and cost, and its composition should be optimized. Fermentation mode (batch, fed-batch and continuous) and substrate feeding strategy (in fed-batch and continuous cultures) affect cell density, specific productivity, volumetric productivity, final product titer and byproduct formation. Scale-up studies are essential, considering nutrient feeding, mixing, aeration and cooling challenges. Downstream processes, including product recovery and purification, can also benefit by reducing byproduct formation through metabolic engineering and by adopting innovative unit operations. Additionally, well-established process optimization strategies from chemical engineering, combined with AI and data science, can be employed to optimize the entire bioprocess. Taken together, chemical engineers will play an increasingly significant role in developing bioprocesses for the sustainable production of various chemicals, addressing the challenges associated with the climate crisis, sustainability, health, food and the environment.
Kevin M. Van Geem: empowering reaction engineering for a net-zero chemical industry
The twenty-first century holds the potential to be the era of the chemical engineer. We face unprecedented challenges, including climate change, increasing energy needs and pervasive pollution. Chemical engineers play a pivotal role as they adapt to the dynamic landscape of technology, sustainability and global issues, steering us towards innovative solutions for a sustainable and interconnected world. Key is understanding the reactions, that is, avoiding the unwanted ones and accelerating the desired ones. This subfield of chemical engineering is better known as reaction engineering, and it has surely come of age 33 . Understanding the intricate interplay of various factors, including flow dynamics, heat and mass transfer, and reaction kinetics, takes center stage in establishing the correlation between reactor performance and input composition and operational conditions. Initially applied within the realms of the petroleum and petrochemical industries, this versatile methodology can be effectively employed to optimize a broad spectrum of systems necessitating the modeling or engineering of reactions. Chemical reaction engineering methodologies are, in essence, finely tuned for both the development of innovative processes and the enhancement of pre-existing technological frameworks.
Transitioning from traditional fossil-based resources to sustainable alternatives poses a significant hurdle. For large-scale processes, such as thermochemical conversion of plastic waste, there is no doubt that reaction engineering has and will continue to make important contributions. The complexity of plastic waste is like that of oil; aspects of accurate feed characterization, measuring intrinsic kinetics and modeling of those reactive systems can almost be considered as ‘business as usual’. One key step that needs to be taken is that modeling approaches developed by reaction engineers must become predictive instead of postdictive. In this context, machine learning could be a key enabler 34 . Essential is the availability or capability to generate large, clean datasets. Owing to the cost of real experiments, these large quantities of data are usually obtained via simulations, and with continuously increasing computational power, more high-level datasets can be generated. However, the integration of digital technologies, automation and machine learning into reaction engineering processes demands expertise. Additionally, managing and interpreting the vast amounts of data generated in modern processes is a critical challenge. Striking a balance between optimizing reaction efficiency and adhering to stringent safety and regulatory standards further complicates the landscape for chemical reaction engineers in the twenty-first century.
A second aspect where reaction engineers can drive innovation is by combining detailed chemistry of typically hundreds of reactions in computational fluid dynamics. Today, computational fluid dynamics often starts from a postdictive basis by parameter tuning to predict experimental data, evolving to a predictive basis once sufficient robust validation is performed 35 . However, substantial process intensification is possible by combining first-principles-based models with computational fluid dynamics 36 . Continued development of computational chemistry methods for predicting reaction networks and pathways, reaction rate parameters, thermophysical properties and structure−property relationships should accelerate the decision-making and development timelines for many reaction systems. More broadly, as computer power continues to grow, reaction engineers can grow their ability to include increasing levels of complexity in multiscale models. At the same time, reaction engineers should prudently incorporate machine learning into data analysis and hybrid models for workflows from early-stage molecular simulations to reactor scale-up and optimization models. This makes reaction engineering excellently positioned to drive the developments of so-called integrated reactors such as membrane reactors, chemical looping processes and sorption-enhanced processes. In addition, the implementation of alternative energy sources for reactors, such as plasma, microwave, light, ultrasound and Joule (resistive) heating, can contribute to the enhancement and cost reduction of reactive processes 37 .
Perhaps the biggest challenge that we all face is becoming net zero. In this context, ‘hydrogen’, but more general ‘electrification of the chemical industry’, is considered the silver bullet. However, it is accompanied by a multitude of intricate scientific and technological hurdles that demand resolution and where reaction engineering will play a key role. For example, electrochemical reactor design faces numerous challenges such as electrode durability, overall efficiency and cost. However, the drive to go to an e-chemistree 37 is huge, not only from a sustainability perspective but also from a geopolitical point of view. Just in Europe, more than 800 million tons of oil is consumed each year, which makes this continent extremely dependent. Therefore, there is strong interest in e-fuels and e-chemicals, such as ammonia, hydrogen and methanol. By innovating in areas such as the creation of novel materials and catalysts, as well as exploring dynamic reactor operation and catalysis acceleration through dynamic catalysis, reaction engineering will further boost its impact 38 .
With the multitude of challenges confronting the world, the twenty-first century seems poised to become the era of engineering, with a pivotal role for chemical engineering.
Jean Tom: producing pharmaceuticals at scale for improved human health
Recent milestones from the pharmaceutical industry, such as the production of COVID-19 vaccines and a cure for hepatitis C infections, highlight the importance of new medicines to improve human health through prevention, treatment and cure of diseases. Chemical engineers play a vital role in linking research in drug discovery to the production of medicines that can be accessed by patients worldwide. Penicillin, a relatively simple small-molecule drug discovered in 1928, was not widely available until the early 1940s after chemical engineers designed the process and equipment (deep-tank fermentation, filtration, extraction and crystallization) to enable manufacturing. Now, as the diversity and complexity of therapies grow, there are many opportunities for chemical engineers to advance and accelerate innovations in human health.
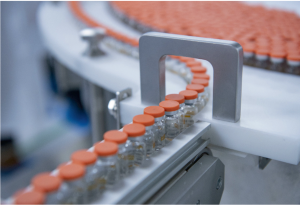
Historically, chemical engineers focus on the process, designing unit operations such as reactions, distillations, extractions, crystallizations, fermentations and granulations to produce pharmaceuticals at an industrially relevant scale by applying the principles of thermodynamics, transport processes, kinetics, separations and process control. The focus has long been on small-molecule drugs (<1 kDa) and biologics (including vaccines) (>5 kDa). However, the distinction between small-molecule and biologics development has become progressively blurred as many of the new modalities sit at this interface: conjugation of small molecules to biologics, enzymes to synthesize small molecules, and peptides that integrate recombinant and synthetic approaches. Advances in molecular biology in the past decades have led to new therapies where the patient’s cells or genes are treated directly. Chemical engineers can apply the same foundational principles in these therapies to the extraction, separation, genetic modification, growth and return of the patient’s cells. While the science of new therapies is evolving to incorporate more biology, the role and importance of chemical engineers in this field will continue to drive the development of the manufacturing processes. The impact of engineering in the pharmaceutical industry will be maximized by the expanding overlap and collaboration between chemical engineering and biomolecular and biological engineering 39 .
In recent years, the chemical engineer’s role has expanded beyond process engineering to also include drug discovery, therapy design, synthetic chemistry, biological pathway development and drug delivery. This has been accompanied by major developments in process automation, high-throughput experimentation, modeling, and large datasets that are now ubiquitous. New approaches to process modeling and prediction of outcomes are enabling the transformation of the large volume of data into knowledge about trends that can lead to new synthetic designs and biological pathways as well as new drug targets and molecules 40 . At the same time, these tools and approaches, applied with sound physics-based understanding of unit operations, are transforming how chemical engineers invent, develop and characterize the processes and accelerate bringing drugs to market. As one of the key drivers in process development is sustainability, chemical engineers will also be at the forefront to translate new sustainable approaches to build complex molecules using novel photo-, bio- and electro-catalytic chemistry 41 .
As chemical engineers in industry work across a wider range of therapeutic modalities and throughout the broader pharmaceutical enterprise (discovery, process development and manufacturing), they will be working with a much more dynamic and cross-functional group of researchers in the future than they have done in the past. The pharmaceutical industry and the chemical engineering academic community need to partner to both accelerate technology solutions and prepare students to enter the workforce. There are opportunities in pre-competitive collaborations 42 , where pharmaceutical companies partner to identify common challenges and work with academic researchers to solve. Chemical engineers entering the industry must continue to have a strong foundation in the chemical engineering principles and its physics-based understanding. Having a curriculum that combines the core chemical engineering competency and a fluency in the natural sciences with the ability to apply computational and modeling skills will enable chemical engineers to be key contributors to advancing and accelerating innovations in human health.

Gaohong He: designing advanced membrane materials to mitigate climate change
The separation of mixtures into pure components is extremely important in industrial chemical processes, which often consumes large amounts of energy and can accelerate climate issues such as the generation of greenhouse gases 43 . British economist Nicholas Stern pointed out in the Stern Report published in 2006 that the ever-increasing greenhouse effect will seriously affect global economic development, and its severity will be no less than that of the First and Second World Wars and the Great Depression. Directly or indirectly solving environmental problems requires efficient and large-scale separations, beyond the laboratory level, firmly into the field of chemical engineering. Membrane separation technology stands out among many separation technologies because it does not require phase changes, consumes relatively low amounts of energy and couples to other processes relatively easily. Chemical engineers have long coupled membrane-based technology with other processes to realize various applications in the liquid phase (such as desalination, pervaporation and water treatment) and the gas phase (such as carbon capture and hydrogen recovery).
Carbon capture, utilization and storage (CCUS) is a key technology to address global climate change 44 . Membrane-based gas separation technology can potentially replace traditional energy-intensive separation processes, which is important for net-zero developments. To achieve energy savings and emission reductions from these gas-phase separations, a variety of new membranes and materials must be designed and optimized by chemical engineers, especially the development of advanced gas separation membranes that largely dictate the overall separation efficiency. Conventional polymer membrane materials usually do not possess regular and continuous sub-nanometer channels and are limited by a trade-off between gas permeability and selectivity. However, emerging porous crystalline nanomaterials have great potential to overcome these limitations 45 , including metal–organic frameworks (MOFs), covalent–organic frameworks (COFs) and hydrogen-bonded organic frameworks (HOFs) 46 . In these materials, sub-nanometer solid-state channels can enable the selective transport of small gas molecules. The main design principle is still that structure largely determines performance. Advanced membrane structures should continue to be explored along four considerations: designing superior functional nanomaterials; modulating the polymer matrix performance; designing synergistic unification between the porous fillers and polymer matrix; and building highly efficient mass-transfer pathways in the membrane materials.
Mixed matrix membranes, for example, combine the excellent transport properties of porous materials with the processability of polymers 47 . Chemical engineers could gradually investigate the basic structure of the material and then consider applications for industrial scale-up. The physicochemical microenvironment of nanomaterials can be regulated using functional modifications, pore modulation and constructional defects to enhance adsorption to satisfy specific sieving. As for the polymeric matrices, rational regulation through modulation of properties, such as free volume and chain rigidity, should also be key considerations for the development of advanced materials. In addition to the modulation of the material properties, it is also possible to optimize the filler–polymer interfacial interactions and build low-resistance mass-transfer pathways in membranes to induce fast and efficient transport of gas molecules. The further industrial expansion of mixed matrix membranes can proceed from defect-free, thin, selective layered structures, which require the development of new synthetic procedures.
Inorganic membranes are also a burgeoning research avenue due to their excellent gas permeabilities and stabilities. Multicrystalline composite membranes are a relatively new example, which are typically composed of uninterrupted porous nanocrystalline layers on an inorganic support substrate. The sub-nanometer multicrystalline materials provide more designability and modulation from multiple perspectives such as adsorption and sieving. To escape the limitation of the high cost of inorganic substrates to enable more feasible industrialization, an alternative form of organic–inorganic association is also being explored, which utilizes a flexible polymer substrate as a support for the construction of polycrystalline sub-nanometer molecular channels that provide separation. Chemical engineering requires consideration of practical applications, not only for the modulation of material properties but also for the limitations of industrial scale-up conditions, such as cost and operability.
In summary, advanced membrane material design must be a key focus of chemical engineering research to mitigate climate change and achieve targeted energy-efficient gas separations. So far, the introduction of novel functional nanomaterials has further enhanced the designability of membranes through a variety of means across a wide range of scales, from the material itself to the overall structure of the membrane and other aspects of tuning and design. Meanwhile, from the perspective of practical applications, it is necessary to explore new material fabrication methods suitable for controllable scale-up to realize the transition from the laboratory to the industrial scale. Advanced membrane materials require the brainstorming of many to make CCUS more efficient and solve the practical problems we are facing as a society.
Box 1 The contributors
Laura Torrente-Murciano is a professor in reaction engineering and catalysis at the University of Cambridge where she leads the Catalysis and Process Integration Group. Her research focuses on the development of sustainable chemical technologies combining catalysis development, reaction engineering and process integration. She is currently pioneering technologies for the small scale, distributed production of ammonia as a fertilizer, long-term energy vector and fuel, as well as the controllable manufacturing of nanomaterials. She is a member of the UK Catalysis Hub and the Interdisciplinary Centre Energy@Cambridge.
Jennifer B. Dunn is a professor of chemical and biological engineering at Northwestern University. She directs Northwestern’s Center for Engineering Sustainability and Resilience and is the associate director of the Northwestern-Argonne Institute of Science and Engineering. Her research evaluates the environmental and societal effects of emerging technologies including energy storage, hydrogen, sustainable polymers and critical mineral extraction. She co-authored National Academy committee reports on gaseous carbon waste streams utilization and methods for fuel life-cycle analyses. She is an education co-chair of the American Institute of Chemical Engineers Sustainable Engineering Forum.
Panagiotis D. Christofides has been with UCLA since 1996 where he is currently a distinguished professor and department chair in the Department of Chemical and Biomolecular Engineering, a distinguished professor in the Department of Electrical and Computer Engineering and the holder of the William D. Van Vorst Chair in Chemical Engineering Education. His theoretical research interests include nonlinear and predictive control, analysis and control of distributed parameter systems, multiscale systems and hybrid systems, and machine learning and data science, with applications to chemical processes, advanced materials processing, particulate processes, energy, and water systems.
Jay D. Keasling is a professor of Chemical & Biomolecular Engineering and of Bioengineering at the University of California, Berkeley, senior faculty scientist at Lawrence Berkeley National Laboratory, and chief executive officer of the Joint BioEnergy Institute. His research focuses on engineering microorganisms to convert sugar into biofuels, commodity and specialty chemicals, and pharmaceuticals.
Sharon C. Glotzer is the J. W. Cahn Distinguished University Professor of Engineering, the S. W. Churchill Collegiate Professor of Chemical Engineering and the A. C. Lembke Department Chair of Chemical Engineering at the University of Michigan. She is a member of the National Academy of Sciences, the National Academy of Engineering, and the American Academy of Arts and Sciences. Using computer simulation, geometrical concepts and statistical thermodynamics, she designs new materials by exploiting the complex behavior that emerges from simple rules and forces. Her group’s open-source software packages can be downloaded at https://github.com/glotzerlab .
Sang Yup Lee is a distinguished professor at the Department of Chemical and Biomolecular Engineering, KAIST. He is also senior vice president for research at KAIST. He is an elected member of the Korean Academy of Science and Technology and National Academy of Engineering Korea. He is also an international member of both the National Academy of Sciences, USA, and the National Academy of Engineering, USA, as well as a foreign member of the Royal Society, UK. His research interests are metabolic engineering, synthetic biology and industrial biotechnology.
Kevin M. Van Geem is a full professor at Ghent University, leads the Center of Sustainable Chemistry and oversees the Laboratory for Chemical Technology. As the chief technology officer of CAPTURE, he collaborates with more than 40 faculty members across universities to drive radical technological innovations in sustainable resource recovery. His research focuses on reaction engineering, particularly the shift from fossil to alternative resources such as biomass, CO/CO 2 , and plastic waste. He has served in various leadership positions, such as being the chair of the Working Party on Chemical Reaction Engineering of the European Federation of Chemical Engineering (EFCE).
Jean Tom was an executive director at Bristol Myers Squibb where she led a group of chemical engineers focused on development of chemical processes to synthesize small-molecule drug candidates for new therapeutics. Her focus has been to expand the role and impact of chemical engineering in the pharmaceutical industry and bring new approaches to accelerate the generation of process knowledge needed at the different stages of development. She was a founding board member of the Enabling Technologies Consortium, created to advance pre-competitive collaboration for small-molecule development.
Gaohong He is a professor in the Chemical Engineering Department and the director of the State Key Laboratory of Fine Chemicals, Dalian University of Technology, China. She is mainly engaged in the research of membrane separation processes, ion-conducting membranes for energy storage and conversion, and the energy-saving transformations of process industries. Her research interests focus on the rational design of advanced functional nanomaterials for efficient separation and industrial coupling of membrane processes.
Saravanan, A. et al. Chem. Eng. Sci. 236 , 116515 (2021).
Article CAS Google Scholar
Lee, K. et al. Nat. Rev. Chem. 6 , 635–652 (2022).
Article PubMed PubMed Central Google Scholar
Smith, C. & Torrente-Murciano, L. Adv. Energy Mater. 11 , 2003845 (2021).
Sholl, D. S. & Lively, R. P. Nature 532 , 435–437 (2016).
Article PubMed Google Scholar
Smith, C. & Torrente-Murciano, L. Joule https://doi.org/10.1016/j.joule.2023.12.002 (2023).
Torrente-Murciano, L. & Smith, C. Nat. Synth. 2 , 587–588 (2023).
Article Google Scholar
Inventory of U.S. Greenhouse Gas Emissions and Sinks: 1990-2021 https://go.nature.com/46NSDRO (US Environmental Protection Agency, 2023).
Oliveira, A. M., Beswick, R. R. & Yan, Y. Curr. Opin. Chem. Eng. 33 , 100701 (2021).
Arvidsson, R. et al. J. Ind. Ecol. 22 , 1286–1294 (2018).
Liang, C., Gracida-Alvarez, U. R., Hawkins, T. R. & Dunn, J. B. ACS Sustain. Chem. Eng. 11 , 2773–2783 (2023).
Cullen, J. et al. Carbon Clarity in the Global Petrochemical Supply Chain: A Critical Review https://go.nature.com/3NkC2xQ (2022).
Wu, Z., Tran, A., Rincon, D. & Christofides, P. D. AIChE J. 65 , e16729 (2019).
Luo, J. et al. Chem. Eng. Res. Des. 197 , 721–737 (2023).
Wu, Z. et al. Automatica 109 , 108508 (2019).
Chen, S., Wu, Z. & Christofides, P. D. AIChE J. 66 , e16907 (2020).
Suryavanshi, A., Alnajdi, A., Alhajeri, M. S., Abdullah, F. & Christofides, P. D. AIChE J. 69 , e18104 (2023).
Ro, D.-K. et al. Nature 440 , 940–943 (2006).
Article CAS PubMed Google Scholar
Luo, X. et al. Nature 567 , 123–126 (2019).
Srinivasan, P. & Smolke, C. D. Nature 585 , 614–619 (2020).
Article CAS PubMed PubMed Central Google Scholar
Zhang, J. et al. Nature 609 , 341–347 (2022).
Radivojević, T., Costello, Z., Workman, K. & Garcia Martin, H. Nat. Commun. 11 , 4879 (2020).
Hill, P. et al. J. Ind. Microbiol. Biotechnol. 47 , 965–975 (2020).
Glotzer, S. C. & Solomon, M. J. Nat. Mater. 6 , 557–562 (2007).
Boles, M. A., Engel, M. & Talapin, D. V. Chem. Rev. 116 , 11220–11289 (2016).
van Anders, G., Khalid Ahmed, N., Smith, R., Engel, M. & Glotzer, S. C. ACS Nano 8 , 931–940 (2014).
van Anders, G., Klotsa, D., Karas, A. S., Dodd, P. M. & Glotzer, S. C. ACS Nano 9 , 9542–9553 (2015).
Glotzer, S. C. Chem. Eng. Sci. 121 , 3–9 (2015).
Nielsen, J. & Keasling, J. Cell 164 , 1185–1197 (2016).
Kim, G. B., Choi, S. Y., Cho, I. J., Ahn, D.-H. & Lee, S. Y. Trends Biotechnol. 41 , 425–451 (2023).
Lee, S. Y. et al. Nat. Catal. 2 , 18–33 (2019).
Lee, J. A. et al. Trends Biotechnol. 41 , 798–816 (2023).
Bang, J. et al. Adv. Sci. 8 , 2100199 (2021).
Levenspiel, O. Chem. Eng. Sci. 35 , 1821–1839 (1980).
Dobbelaere, M. R., Plehiers, P. P., Van de Vijver, R., Stevens, C. V. & Van Geem, K. M. Engineering 7 , 1201–1211 (2021).
Dixon, A. G. & Partopour, B. Annu. Rev. Chem. Biomol. Eng. 11 , 109–130 (2020).
Ouyang, Y., Heynderickx, G. J. & Van Geem, K. M. Chem. Eng. Process. Process Intensificat. 181 , 109164 (2022).
Van Geem, K. M. & Weckhuysen, B. M. MRS Bull. 46 , 1187–1196 (2021).
Ardagh, M. A., Abdelrahman, O. A. & Dauenhauer, P. J. ACS Catal. 9 , 6929–6937 (2019).
National Academies of Science, Engineering, and Medicine New Directions for Chemical Engineering Ch. 5 (The National Academies Press, 2022).
Chowdhury, A., Joshi, N., Beck, D. A. C. & Pfaendtner, J. Annu. Rev. Chem. Biomol. Eng. 12 , 15–37 (2021).
National Academies of Science, Engineering, and Medicine The Importance of Chemical Research to the U.S. Economy Ch. 4.4 (The National Academies Press, 2022).
Welch, C. J. et al. Org. Process Res. Dev. 21 , 414–419 (2017).
Demirel, S. E., Li, J. & Hasan, M. M. F. Ind. Eng. Chem. Res. 60 , 7197–7217 (2021).
Zheng, W. et al. J. Membr. Sci. 650 , 120330 (2022).
Knebel, A. & Caro, J. Nat. Nanotechnol. 17 , 911–923 (2022).
Wang, Y. et al. Energy Environ. Sci. 16 , 53–75 (2023).
Qian, Q. et al. Chem. Rev. 120 , 8161–8266 (2020).
Download references
Author information
Authors and affiliations.
Department of Chemical Engineering and Biotechnology, University of Cambridge, Cambridge, UK
Laura Torrente-Murciano
Chemical and Biological Engineering, Center for Engineering Sustainability and Resilience, Northwestern University, Evanston, IL, USA
Jennifer B. Dunn
Department of Chemical and Biomolecular Engineering, University of California, Los Angeles, Los Angeles, CA, USA
Panagiotis D. Christofides
Department of Chemical & Biomolecular Engineering, University of California, Berkeley, Berkeley, CA, USA
Jay D. Keasling
Department of Bioengineering, University of California, Berkeley, Berkeley, CA, USA
California Institute of Quantitative Biosciences (QB3), University of California, Berkeley, Berkeley, CA, USA
Division of Biological Systems and Engineering, Lawrence Berkeley National Laboratory, Berkeley, CA, USA
Joint BioEnergy Institute, Emeryville, CA, USA
Center for Biosustainability, Danish Technical University, Lyngby, Denmark
Center for Synthetic Biochemistry, Shenzhen Institutes for Advanced Technologies, Shenzhen, China
Department of Chemical Engineering, University of Michigan, Ann Arbor, MI, USA
Sharon C. Glotzer
Metabolic and Biomolecular Engineering National Research Laboratory, Systems Metabolic Engineering and Systems Healthcare Cross-Generation Collaborative Laboratory, Department of Chemical and Biomolecular Engineering (BK21 four), BioProcess Engineering Research Center, Korea Advanced Institute of Science and Technology (KAIST), Daejeon, Republic of Korea
Sang Yup Lee
Laboratory for Chemical Technology, Department of Materials, Textiles and Chemical Engineering, Faculty of Engineering and Architecture, Ghent University, Ghent, Belgium
Kevin M. Van Geem
Chemical Process Development, Global Product Development and Supply, Bristol Myers Squibb, New Brunswick, NJ, USA
State Key Laboratory of Fine Chemicals, R&D Center of Membrane Science and Technology, School of Chemical Engineering, Panjin Institute of Industrial Technology, Liaoning Key Laboratory of Chemical Additive Synthesis and Separation, Dalian University of Technology, Dalian, Liaoning, China
You can also search for this author in PubMed Google Scholar
Corresponding authors
Correspondence to Laura Torrente-Murciano , Jennifer B. Dunn , Panagiotis D. Christofides , Jay D. Keasling , Sharon C. Glotzer , Sang Yup Lee , Kevin M. Van Geem , Jean Tom or Gaohong He .
Ethics declarations
Competing interests.
J.D.K. has financial interests in Amyris, Ansa Biotechnologies, Apertor Pharma, Berkeley Yeast, BioMia, Cyklos Materials, Demetrix, Lygos, Napigen, ResVita Bio, and Zero Acre Farms. L.T.-M., J.B.D., P.D.C., S.C.G., S.Y.L., K.M.V.G., J.T. and G.H. declare no competing interests.
Rights and permissions
Reprints and permissions
About this article
Cite this article.
Torrente-Murciano, L., Dunn, J.B., Christofides, P.D. et al. The forefront of chemical engineering research. Nat Chem Eng 1 , 18–27 (2024). https://doi.org/10.1038/s44286-023-00017-x
Download citation
Published : 11 January 2024
Issue Date : January 2024
DOI : https://doi.org/10.1038/s44286-023-00017-x
Share this article
Anyone you share the following link with will be able to read this content:
Sorry, a shareable link is not currently available for this article.
Provided by the Springer Nature SharedIt content-sharing initiative
Quick links
- Explore articles by subject
- Guide to authors
- Editorial policies
Sign up for the Nature Briefing newsletter — what matters in science, free to your inbox daily.


COMMENTS
Chemical engineering is a branch of engineering that deals with the processes (production, transformation, transportation and usage) necessary to produce useful materials and energy. Chemical ...
Dec 2024. Niyaz Mohammad Mahmoodi. Prof. Dr. Mahmoodi was ranked in Stanford University study of the world's top 2% of scientists in 2023 (Rank = 38 in Chemical Engineering). He published 228 peer ...
The journal is especially interested in papers that extend the boundaries of traditional chemical engineering. The journal publishes regular special issues focusing on specific topics, and issues dedicated to selected papers from major conferences. Core topic areas: Distillation and absorption. • Sustainable process design, operation and ...
An International Journal of Research and Development. The Chemical Engineering Journal focuses upon seven aspects of Chemical Engineering: Applied Biomaterials and Biotechnologies, Catalysis, Chemical Reaction Engineering, Computational Chemical Engineering, Environmental Chemical Engineering, …. View full aims & scope.
Launched in January 2024, Nature Chemical Engineering is an online-only journal covering the most significant research and analysis of relevance to the diverse community of chemical engineers.
In this virtual issue, The Canadian Journal of Chemical Engineering (CJCE) features recently published articles (2021 and 2022) on topics that are currently relevant within the chemical engineering community, from the biodegradation of microplastics to tissue engineering. As part of CJCE's 100th volume celebration, this special virtual issue highlights cutting-edge research from authors who ...
To mark the inaugural issue of Nature Chemical Engineering, we asked a collection of scientists working in different branches of chemical engineering to share their perspectives on the challenges ...
From 2013-2021 David was the School Chair of Chemical & Biomolecular Engineering at Georgia Tech. David's research uses computational materials modeling to accelerate development of new materials for energy-related applications and carbon dioxide mitigation. He has published over 370 papers that have received over 21,000 citations.
Trending Topics in Chemical Engineering: 2022-2024. First published: 7 February 2024. Last updated: 14 February 2024. This virtual issue features articles from recent years that have piqued the interest of the chemical engineering community. The following articles have garnered attention through elevated reads, downloads, and citations.
International Journal of Chemical Engineering is an open access journal publishing research focused on technologies for the production, processing, transportation and use of chemicals on an industrial scale. As part of Wiley's Forward Series, this journal offers a streamlined, faster publication experience with a strong emphasis on integrity.